Spark plugs
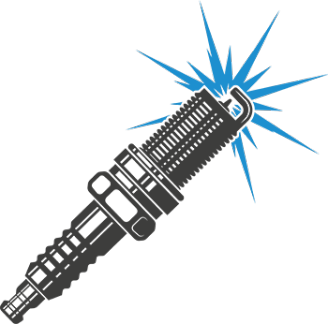
Don’t just learn. Learn smarter, thanks to our exclusive modular educational content. E-Learning in greater detail than ever before, for the ultimate in automotive knowledge
Principles
The igniting spark
The spark plug plays a vital role in the petrol engine. It is responsible for igniting the air-fuel mixture. The quality of this ignition directly affects several factors which are of great importance for both the quality of the driving experience and the environment. This includes starting, smooth running, general engine performance and efficiency as well as the reduction of harmful emissions.
When one considers that a spark plug must ignite a fresh charge of air and fuel between 500 and 3500 times per minute, it becomes clear how difficult the spark plug’s job is and how important the contribution of spark plug technology is for adherence to current emissions standards and to the reduction of fuel consumption.
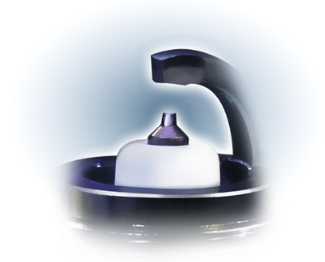
Function of a petrol engine
Ambient air is drawn into the cylinder in the petrol engine. Fuel is also supplied by means of the fuel injection or carburettor. A combustible mixture is therefore formed and is then ignited by the ignition spark. Here you can see the function of a current four-stroke engine schematically:
1. Intake: The piston moves downwards creating a low pressure area. Air and fuel are therefore drawn in through the intake valves.
2. Compression: The pistons move upwards again greatly compressing the mixture. Ignition of the gasses takes place as the piston approaches top dead centre.
3. Power: The temperature of the burning gasses in the combustion chamber rapidly increases up to 2600°C and the pressure increases to up to 120 bar. The piston is pushed down towards the crankshaft at speeds of up to 20 metres per second.
4. Exhaust: The burnt gasses leave through the exhaust valve on the next upward movement of the piston in the cylinder.
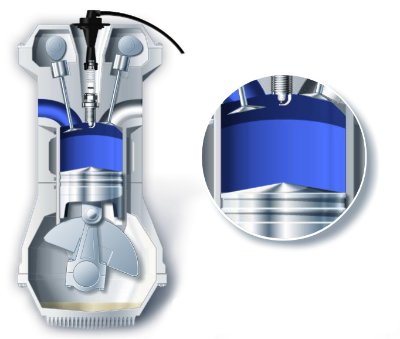
Installation point of the spark plug
The spark plug is screwed into the cylinder head.
The upper part of the plug, visible from the outside of the engine is the electrical connection point. Depending on the applied technology, either the spark plug cover/connector of the high tension ignition cable is pushed onto this connector or – with more modern technical concepts – it may have its own individual ‘pencil’ ignition coil.
The other end of the spark plug protrudes into the combustion chamber and contains the spark electrodes. During engine operation the high voltage applied to the spark plug creates an electric arc between the electrodes. This arc creates an area of intense heat which ignites the air-fuel mixture.
- Electrical terminal
- Intake valve
- Exhaust valve
- Spark electrodes
- Combustion chamber
- Piston
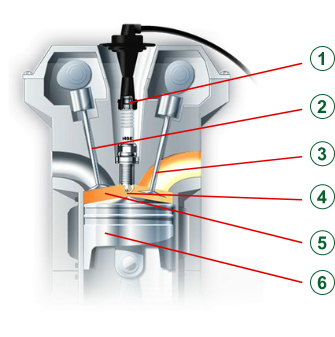
Ignition sequence
Speed
In older systems a central ignition coil generates the high voltage necessary for the ignition of the air-fuel mixture.
A mechanical ignition distributor ensures that this voltage is sent to the correct cylinder’s spark plug at the right time.
The ignition high voltage is fed through a distributor cap and the ignition HT lead which is connected to the spark plug terminal. From here it reaches the tip of the centre electrode and when sufficient voltage is available to overcome the resistance of the air gap between the centre and ground electrode electrical energy discharges to earth in the form of a spark.
In more modern systems an individual ‘pencil coil’ is often fitted directly to each spark plug. With these fully-electronic ignition systems neither mechanical ignition distributors or high-voltage ignition cables are required.
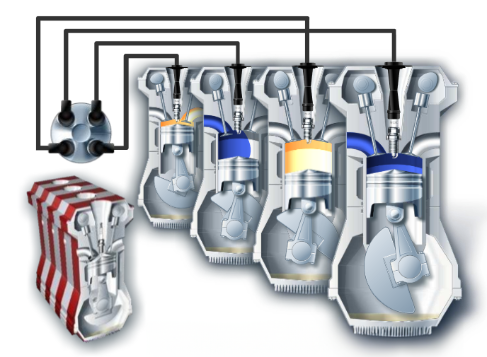
Construction
Connection terminal
The connection terminal is usually an SAE ‘barrel’ shaped connection or a 4mm thread. The high tension ignition lead or a pencil coil is plugged onto the terminal. This connection allows the high voltage to be transferred to the firing end of the spark plug.
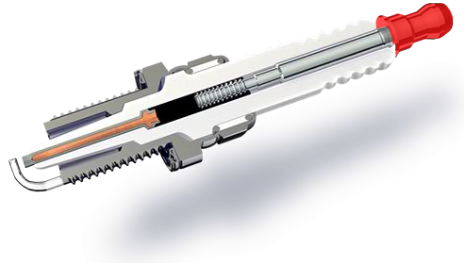
Gasket
The gasket ring prevents any possibility of combustion gas leaking past the spark plug due to the extremely high combustion pressures. In doing this it prevents any cylinder pressure losses.
Another important function is that it provides good conduction of heat to the cylinder head and evens out the different expansion properties of the cylinder head and spark plug housing.
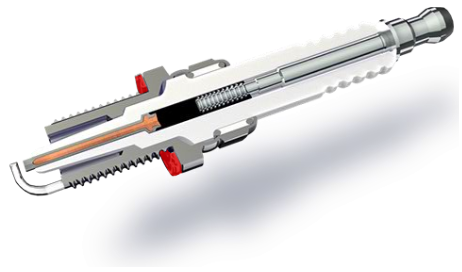
Centre electrode
The centre electrode of a standard spark plug is comprised mostly of a nickel alloy. From the end of this electrode the spark must jump over to the earth electrode. NGK’s spark plugs have a copper core, which significantly improves the thermal conductivity preventing overheating.
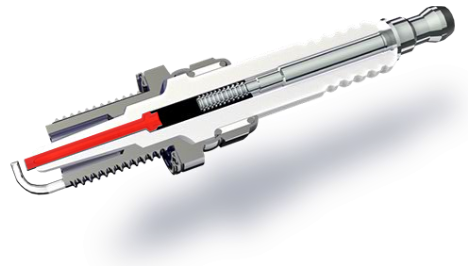
Insulator
The ceramic insulator has two tasks. Its main function is to provide a high degree of electrical insulation preventing the high voltages from discharging to earth externally via the engine casting or other components. It also allows efficient transfer of the heat of combustion from the firing end of the spark plug to the
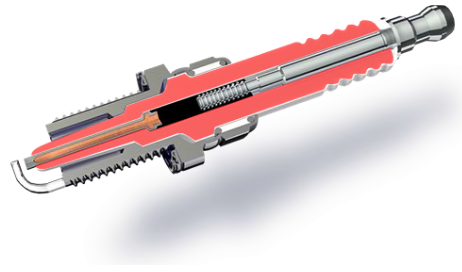
Inner seals
The inner seals create a gas-tight connection between insulator and metal housing. The seal is made from a talcum ring enclosed between two additional stainless steel sealing rings. During production of the spark plug the talc ring is compacted tightly ensuring a perfect gas tight seal.
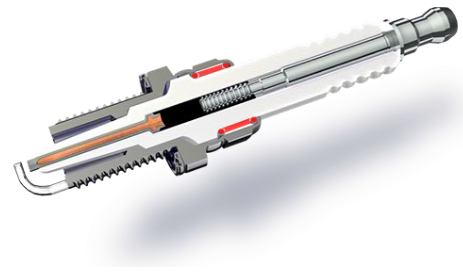
Resistor
In order to ensure electromagnetic compatibility (EMC) and thus the fault-free operation of the onboard electronics, a ceramic resistor is used inside the spark plug as an interference suppression device.
This is constructed by a fusion of carbon and glass compounds which form a solid component within the spark plug. It also prevents interference with electronic components that are not located on the vehicle e.g. domestic TV and radios.
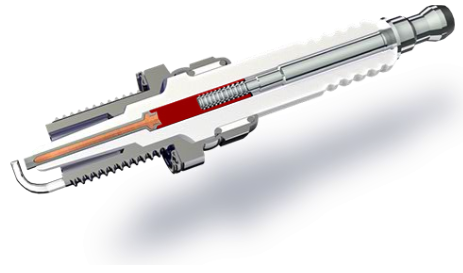
Current leakage barriers
The corrugated current leakage barriers on the outside of the insulator prevent the leakage of electrical energy to the vehicle body earth. They do this by increasing the length of the path that the current would have to travel to reach the earth point provided by the metal shell.
This in effect is like having a significantly taller insulator section ensuring that electrical energy takes the path of least resistance – through the centre electrode.
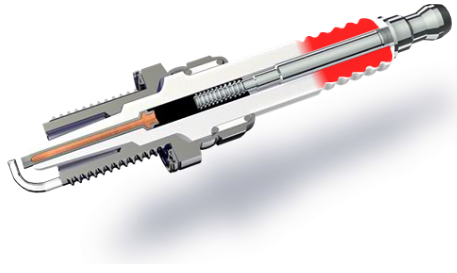
Metal shell
The metal housing or shell also plays an important role in the thermal conductivity of the spark plug as it is part of the mechanism of transferring heat away from the insulator to the cylinder head. The thread on an NGK spark plug is formed by rolling as opposed to being cut. This has the advantage of leaving no sharp edges which can damage the threaded bore in the cylinder head.
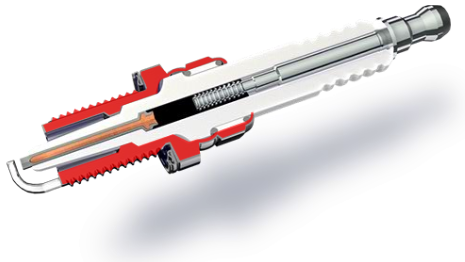
Ground electrode
The earth electrode of a standard NGK spark plug is made of a special nickel alloy. It provides the opposite electrical pole to the centre electrode.
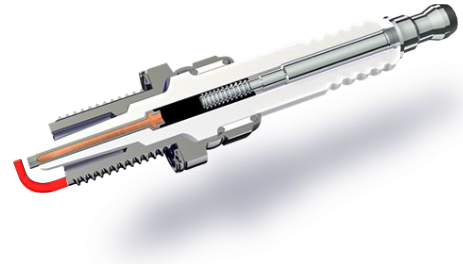
Requirements
The optimal temperature window
In order to maintain efficient operation the firing end of the spark plug must be kept within a certain temperature range.
The lower threshold of this window is a firing end temperature of 450°C, the so-called self-cleaning temperature. Above this temperature threshold, the carbon particles which have collected on the insulator tip are burned off.
Carbon is a by-product of the combustion process and is deposited on surfaces within the combustion chamber and if the operating temperature at the firing end is continuously below 450°C, electrically conductive carbon particles can collect, forming deposits until the ignition voltage flows over the carbon layer to the vehicle earth instead of forming a spark at the gap.
Firing end temperatures above 800°C can heat the electrodes to the point where they start to glow, which can ignite the incoming charge before the spark occurs. This results in uncontrolled ignition leading to abnormal combustion and possible engine damage.
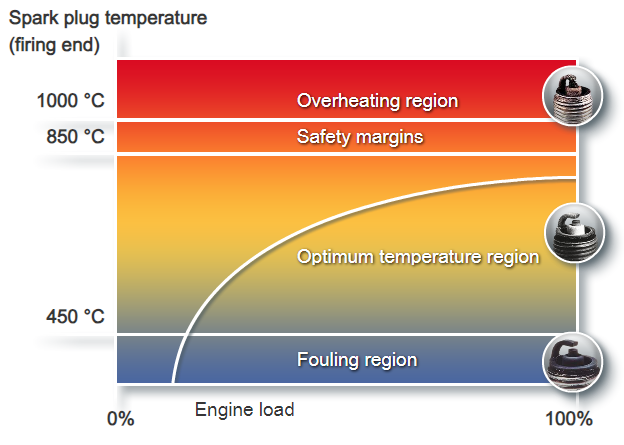
The meaning of the heat rating
The generation of heat varies greatly from engine to engine. For example, a lawn mower will generate less heat than a racing car or a turbocharged engine can run significantly hotter than a naturally aspirated engine.
Therefore a spark plug must be selected that can conduct a precisely defined amount of heat energy to the cylinder head and ensure that the optimal operating temperature range is maintained.
The heat rating of a spark plug provides information about its thermal performance. The following applies for NGK spark plugs: The higher the heat rating number, the higher the thermal performance.
The heat rating number is to be found within the technical part number designation which is marked on the body of NGK’s spark plugs (e.g. BKR6ES).
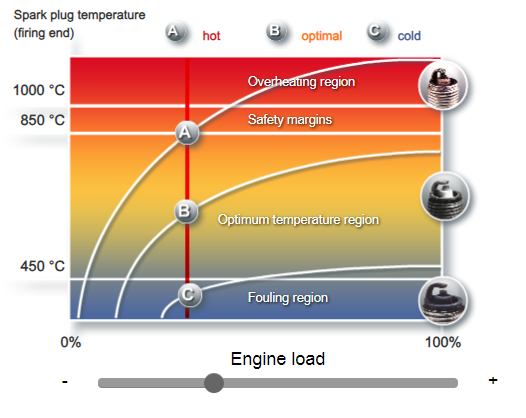
Heat conduction and heat flow
The vast majority of the heat energy transferred away from the centre electrode takes place via the thread and the sealing gasket. A small amount flows away though the external section of the insulator and up the centre electrode.
The insulator absorbs the heat in the combustion chamber and conducts it into the interior of the spark plug. Where the insulator comes into contact with the metal shell, heat is conducted.
Therefore by increasing or decreasing the contact surface area between the insulator and the metal shell the plug’s ability to dissipate more or less heat to the surrounding cylinder head can be selected.
The insulator surface area in the combustion chamber is smaller for spark plugs with higher thermal performance (red shaded area) and for spark plugs with lower thermal performance it is larger.
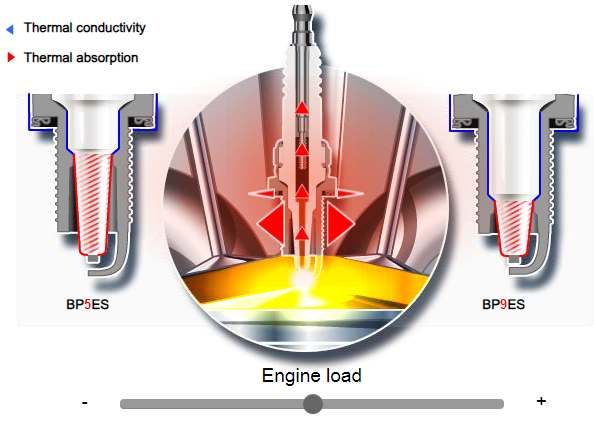
Special requirements
Wear
The replacement intervals for spark plugs as recommended by automobile manufacturers can vary between 20,000 and 120,000 kilometres (12,500 to 75,000 miles.)
This represents a challenge because each time a spark occurs it wears away a microscopic amount of electrode material. Through this "spark erosion" the gap grows and changes shape, increasing the ignition voltage requirement by approximately 500 volts per 20,000 kilometres (12,500 miles).
These effects can be counteracted by the use of multiple ground electrodes and/or the use of wear-resistant electrode materials such as platinum and iridium. Iridium alloys are currently the most modern and erosion-resistant variant.
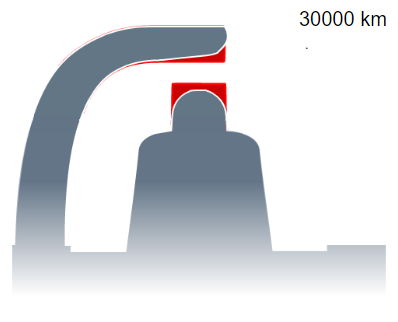
Efficient combustion and emissions
Modern engines must adhere to strict environmental guidelines. Therefore a great challenge lies in improving engine efficiency and the reduction of fuel consumption as well as the reduction of harmful emissions.
Significant reductions in harmful emissions have already been achieved in recent years. In addition carbon dioxide emissions have also been minimised – despite the fact that vehicles have often become heavier.
The reliability of the ignition over the entire service life of the spark plug plays a vital role in the process.
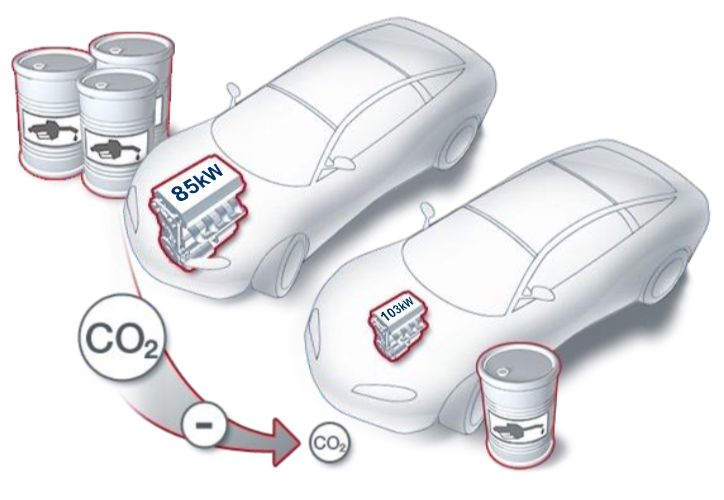
Downsizing
The physical size and cubic capacity of petrol engines is generally becoming smaller whilst the power output is maintained or even increased.
This trend is referred to as "downsizing“ and this strategy offers reductions in both fuel consumption and environmental pollution.
In order to provide the necessary power output such engines are often used in conjunction with some form of pressure charger such as a turbocharger and/or a supercharger (compressor).
In these engines the intake and exhaust valves tend to be larger, as do the engine coolant passageways. This leaves less room available for spark plug installation.
Due to this restriction of space, spark plugs used in these engines typically have a reduced thread diameter of 12mm instead of the more conventional 14mm. The more compact the spark plug, the smaller the wall thickness of the insulator. This presents a challenge for spark plug design as a high dielectric strength must be maintained to cope with the voltage peaks.
- Large spark plug bore
- Insulator ceramic
- Small valve diameter
- Hexagon
- Thread
- Smaller coolant passages
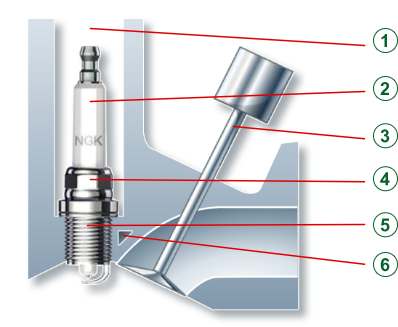
Gas as fuel
Ever more engines are being converted to "bivalent operation". That means: They are being adapted so that they can run on conventional petroleum or a gas (LPG /CNG).
This can have a profound effect on the spark plugs. The combustion of gas is similar to that of normal petrol-fuelling operation however there are some important factors to be considered. The combustion of LPG increases the thermal load on the spark plug increasing firing end temperatures by approx. 80 degrees Celsius or higher.
The air-gas mixture is more difficult to ignite. The ignition voltage requirement is up to 5000 volts higher than with petrol. The entire ignition system, and especially the ignition coils, is placed under considerably increased stress by this increase in voltage requirement.
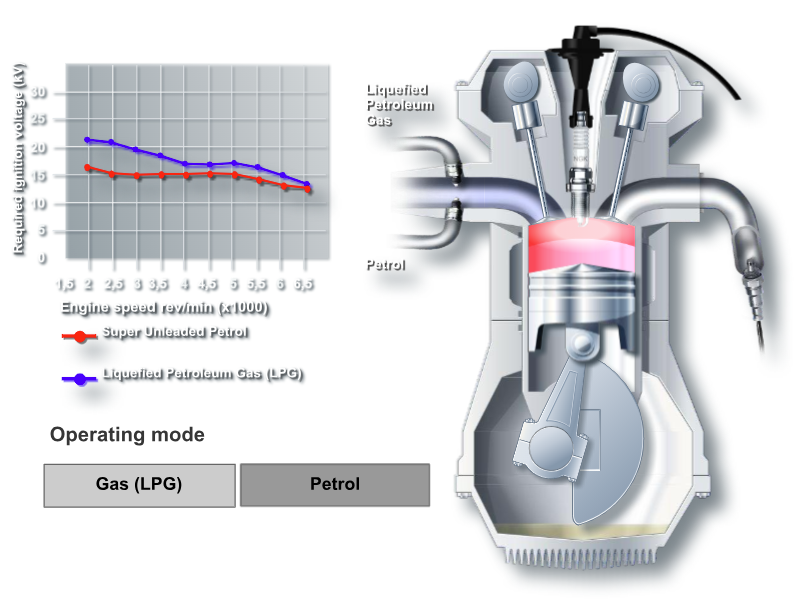
Spark plug types
Spark plugs vary in shape, diameter, thread length, the number and shape of electrodes as well as the electrode materials which are used. Here you can see some of the more important spark plug types currently in use.
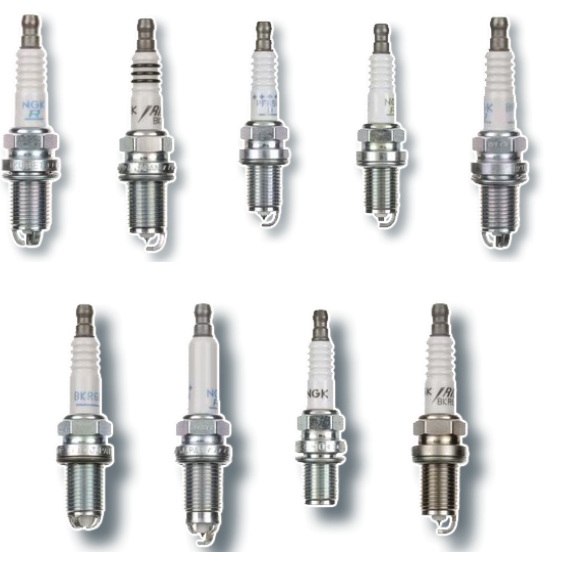
Multiple ground electrode spark plugs
One strategy for extending the service life of a standard spark plug is to equip it with multiple ground electrodes. The spark will of course discharge via the path of least resistance therefore as each electrode wears the spark will discharge to an alternative less worn electrode. This results in the wear being distributed to all available electrodes, reducing overall gap growth and thus extending the service life.
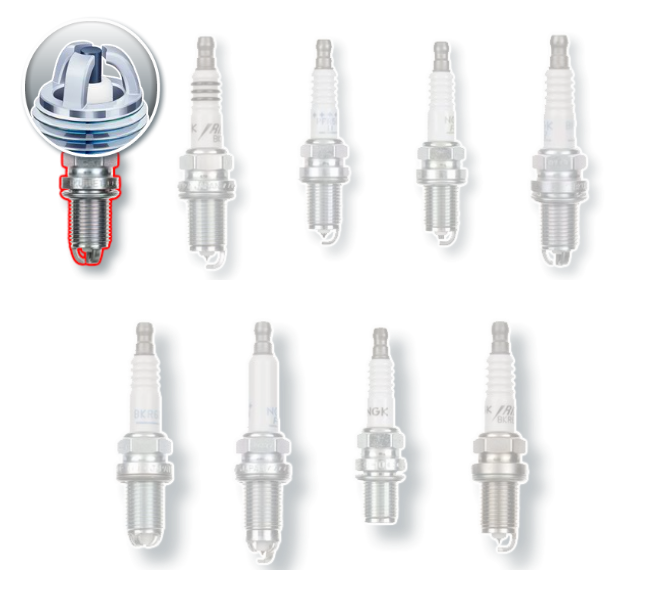
Iridium spark plugs
Iridium spark plugs from NGK currently represent the highest-quality technological solution. They have a small chip of iridium-alloy attached to the centre electrode. This is welded into place by special process using a laser.
The precious (noble) metal iridium is one of the world's hardest metals. It has an extremely high melting point - in excess of 2450°Celsius and is very resistant to spark erosion. Through its use, the service life is on average more than doubled in comparison to standard spark plugs. In addition, the noble metal allows the centre electrode to be designed significantly smaller in diameter, typically 0.6 mm but as low as 0.4mm. These features reduce the ignition voltage requirement considerably and contribute to improving the spread of the flame front in the combustion chamber.
There is also an additional 'self-cleaning effect': Regardless of the current operating temperature, electrical discharges take place in the circular gap between the centre electrode and insulator nose. These discharges burn away any carbon particles which may be present.
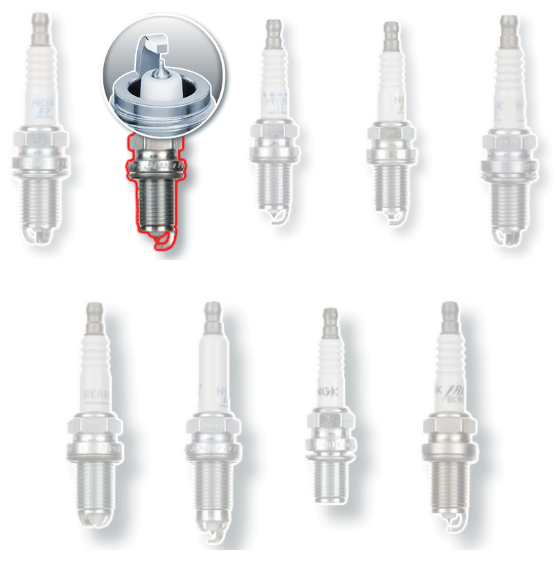
Platinum spark plugs
The use of the precious (noble) metal platinum provides a very hard wearing electrode material allowing a considerable reduction in electrode diameter (typically 0.8mm) without compromising the service life. Due to its ‘fine wire’ centre electrode the spark required voltage is reduced and a more consistent sparking position is provided. Good gas flow around the spark position improving the spread of the flame front in the combustion chamber is another advantage of the fine wire design. In addition many of these plug types have a chip of platinum attached to the ground electrode to further improve the service life.
Platinum is also used on the centre electrode of some multi-ground electrode non-fine wire types to enhance the service life.
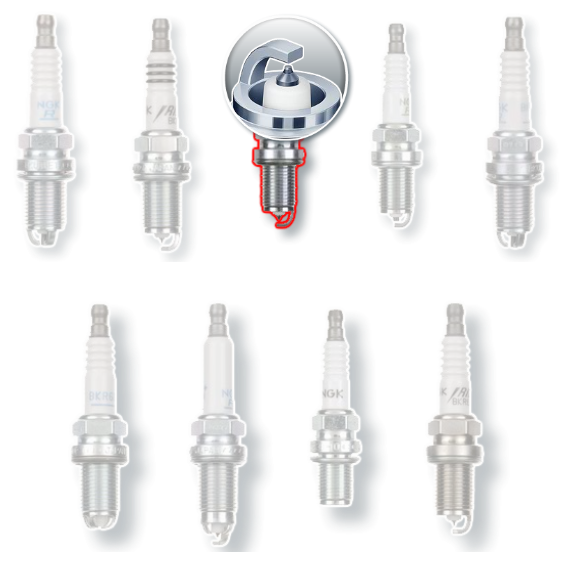
Spark plugs with V-Grooved centre electrode
The centre electrode of this spark plug is provided with a V-shaped indentation across the top face. This forces the spark to occur at the outer edges of the electrode. The spark is more open to the ignitable mixture which for the same time period provides greater flame kernel growth. There is no reduction in service life.
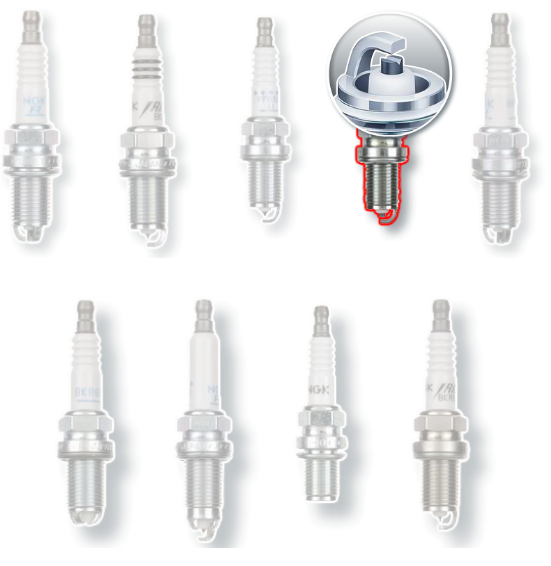
Spark plugs with supplementary spark gap
These spark plugs were developed for engines and operating modes that are subject to higher amounts of carbon deposition. Spark plugs with supplementary spark gaps are equipped with a metal shell design that extends towards the insulator nose. If excessive carbon has become deposited on the insulator nose and the engine is started, the tendency is that the spark current will find the path of least resistance and flow over the carbon to reach earth rather than jump the intended spark gap.
However as the metal shell is extended towards the insulator the small gap between the two presents an easier electrical path than travelling to the base of the insulator. The spark discharges to the metal shell and thus the ignition of the air-fuel mixture continues to occur. As soon as the spark plug reaches the self-cleaning temperature of 450°C, carbon deposits are burned off and the spark can reassume the normal path to earth via the ground electrode.
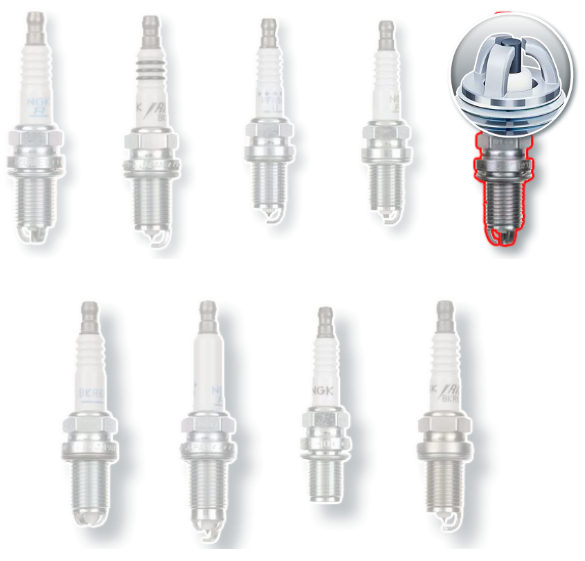
Semi-surface discharge type spark plugs
These spark plugs provide for reliable cold start when there are carbon deposits fouling the insulator and even clean the insulator at temperatures below the self-cleaning temperature.
To achieve this they have at least two ground electrodes arranged at the sides of a tapered insulator nose. If the insulator is clean, the spark takes place between the tip of the centre electrode and the tip of one of the ground electrodes towards the outer end.
If the insulator is fouled with carbon deposits, the spark initially creeps over to the insulator nose but then arcs over to the lower end of the ground electrode as this presents an easier path than creeping over on the entire insulator to earth.
With this process, not only is the air-fuel mixture ignited, but the tip of the insulator nose is also cleaned of carbon deposits by the action of the spark. By virtue of this process a normal arc-over between the centre and ground electrode takes place.
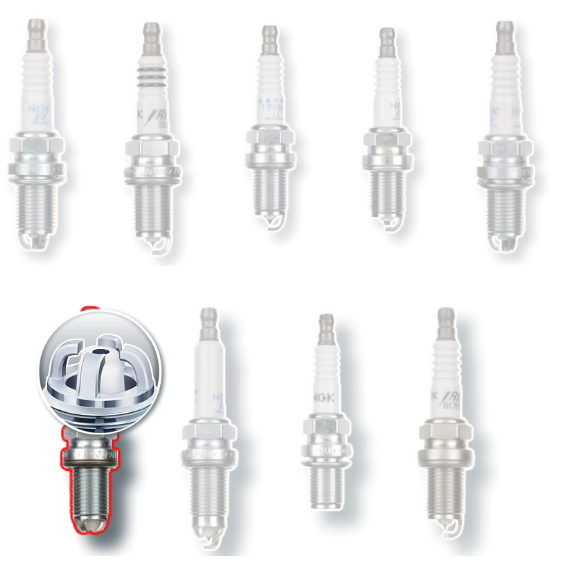
Hybrid spark plugs
Hybrid technology was developed for engines which tend towards increased carbon deposition as a result of their design. They combine the features of both fine centre electrode platinum spark plugs as well as semi-surface discharge type spark plugs. They have a 'normal' ground electrode as well as two smaller auxiliary ground electrodes to the side.
The small diameter platinum electrode keeps the ignition voltage requirement down and ensures an optimal spread of the flame front. Thanks to the resilience of platinum, the electrode gap remains nearly constant over the entire service life. The semi-surface discharge technology ensures an optimal cold start in the case of carbon fouling and for the removal of carbon deposits even at temperatures below the self-cleaning temperature.
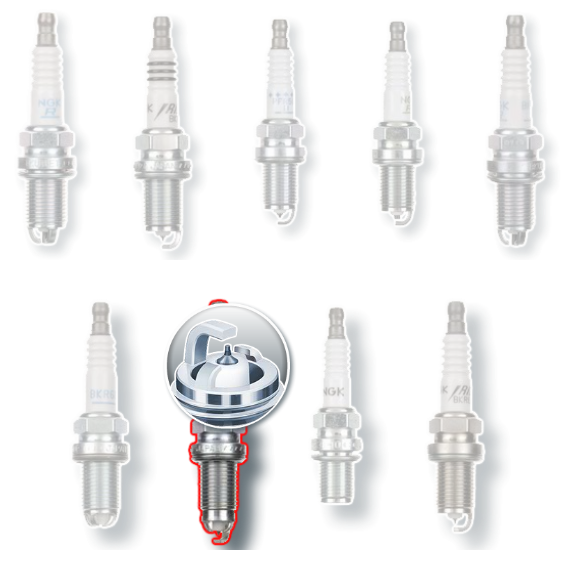
Racing spark plugs
Spark plugs used for racing must be able to withstand the extreme stresses experience in high performance engines. Engine speeds change very rapidly and in some applications can frequently exceed 15,000 rpm. Temperature, pressure, vibrations and turbulence in the combustion chamber are so immense that conventional earth electrodes could break or overheat.
For this reason, racing spark plugs used in the most extreme environments such as F1 are designed with a circular ground electrode. The spark creeps from the centre electrode over the insulator nose to the ground electrode instead of<br>jumping an air gap.
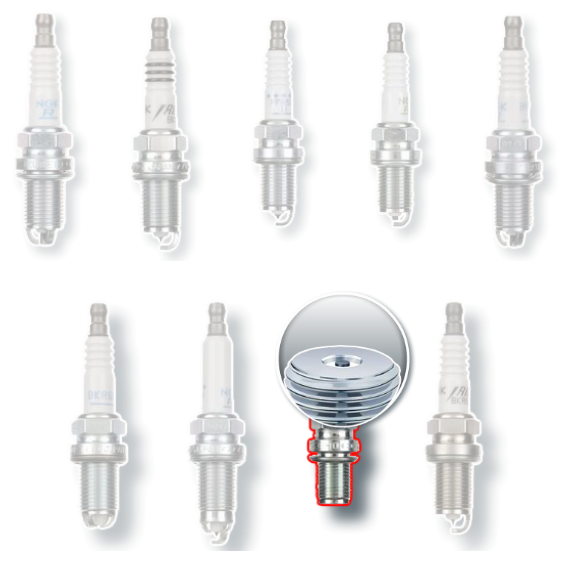
LPG/CNG spark plug
LPG Laser Line spark plugs are double precious metal types that were specifically developed for gas-fuelled engines. Their centre electrode has a tip made of iridium and a chip of platinum is used in the ground electrode. Both precious metals are very resistant to spark erosion despite the higher ignition voltages required in gas-fuelled operation. An additional special copper core in the ground electrode also provides optimal heat conductivity and the metal shell has a coating of nickel alloy to protect against the higher corrosion experienced in gas powered engines.
These spark plugs also accommodate the higher ignition voltage requirement in gas-fuelled operation. Thanks to a centre electrode diameter of 0.6 mm, they require less ignition voltage to create the spark and thus reduce the stress on the ignition coils. For a further reduction of the ignition voltage requirement, they have a factory pre-set electrode gap of 0.8 mm.
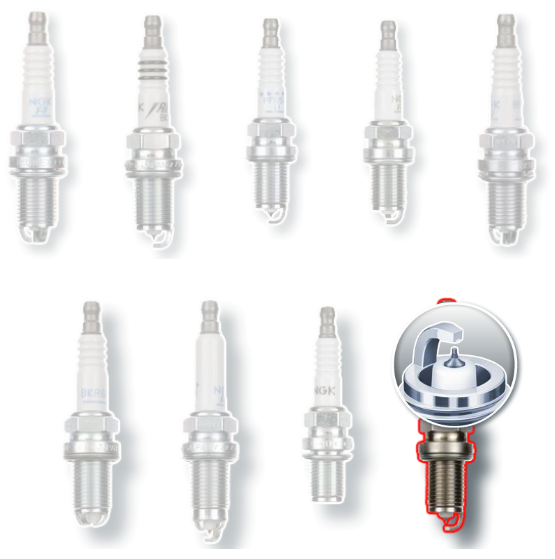
Spark plugs in action
Spark plugs vary in shape, diameter, thread length, the number and shape of electrodes as well as the electrode materials which are used. Here you can see some of the more important spark plug types currently in use.

Spark plugs with V-Grooved centre electrode
The centre electrode of this spark plug is provided with a V-shaped indentation across the top face. This forces the spark to occur at the outer edges of the electrode. The spark is more open to the ignitable mixture which for the same time period provides greater flame kernel growth. There is no reduction in service life.
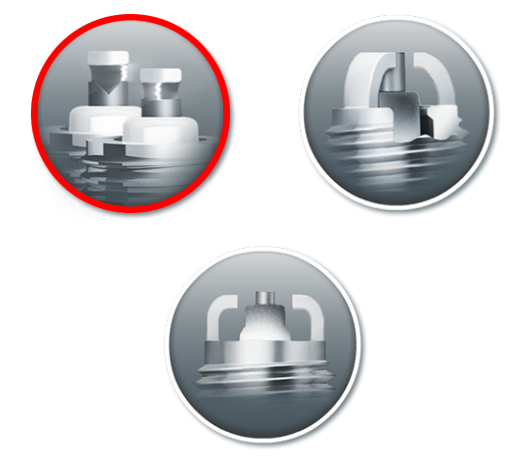
Spark plugs with supplementary spark gap
These spark plugs were developed for engines and operating modes that are subject to higher amounts of carbon deposition. Spark plugs with supplementary spark gaps are equipped with a metal shell design that extends towards the insulator nose. If excessive carbon has become deposited on the insulator nose and the engine is started, the tendency is that the spark current will find the path of least resistance and flow over the carbon to reach earth rather than jump the intended spark gap.
However as the metal shell is extended towards the insulator the small gap between the two presents an easier electrical path than travelling to the base of the insulator. The spark discharges to the metal shell and thus the ignition of the air-fuel mixture continues to occur. As soon as the spark plug reaches the self-cleaning temperature of 450°C, carbon deposits are burned off and the spark can reassume the normal path to earth via the ground electrode.
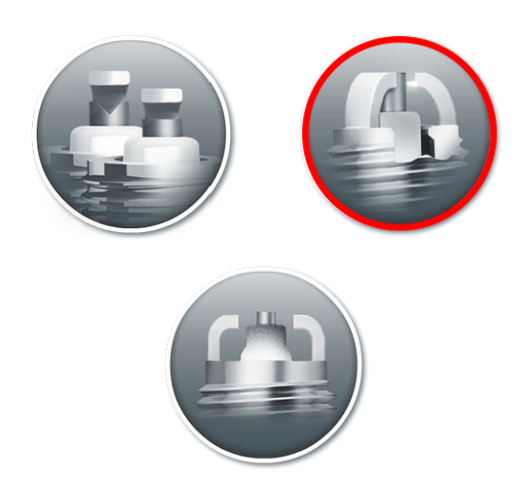
Multiple ground electrode spark plugs
One strategy for extending the service life of a standard spark plug is to equip it with multiple ground electrodes. The spark will of course discharge via the path of least resistance therefore as each electrode wears the spark will discharge to an alternative less worn electrode. This results in the wear being distributed to all available electrodes, reducing overall gap growth and thus extending the service life.
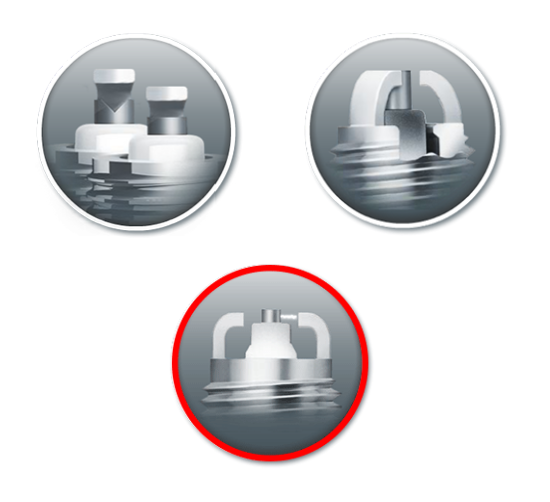
Installation
The right torque
A torque wrench is required for the correct installation of a spark plug. Even for a professional technician the estimation of the tightening torque is virtually impossible.
This is because torque is calculated by the multiplication of two factors: the force which is applied and the distance at which that force is applied relative to the centre of rotation.
Most spark plug failures can be traced back to an incorrect tightening torque. If it is set too low, there is a risk of compression loss and plug overheating. It is also possible that the insulator or centre electrode may also be damaged as a result of excess vibration.
If the tightening torque is set too high, the spark plug metal shell will be over stressed and possibly yield. The shell can also expand or distort. The distortion causes the heat dissipation zones to be disrupted, overheating and melting of the electrodes or even engine damage can occur.
Illustration of how tightening torque values applied to an M14 spark plug in an aluminum cylinder head affect the spark plug
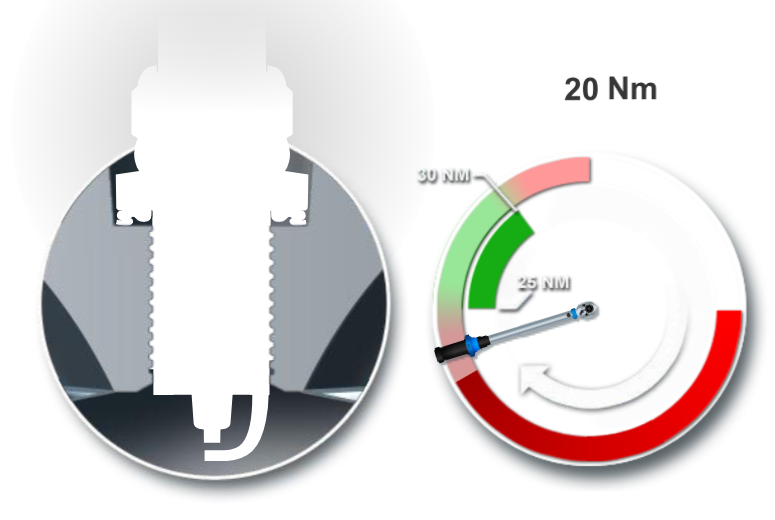
Overview of torque settings
The torques depend on the cylinder head material and the thread diameter.
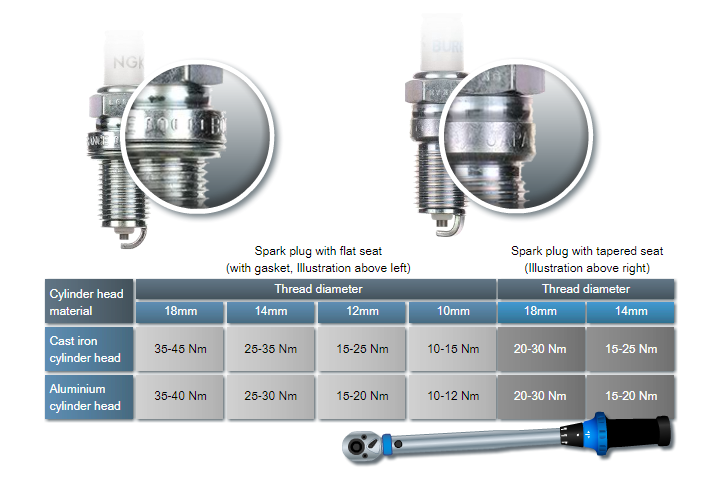
Installation video
Take a look over the shoulder of an NGK SPARK PLUG professional.
You will see that by paying attention to all the important steps in the procedure, the installation of spark plugs can be performed quickly and safely.
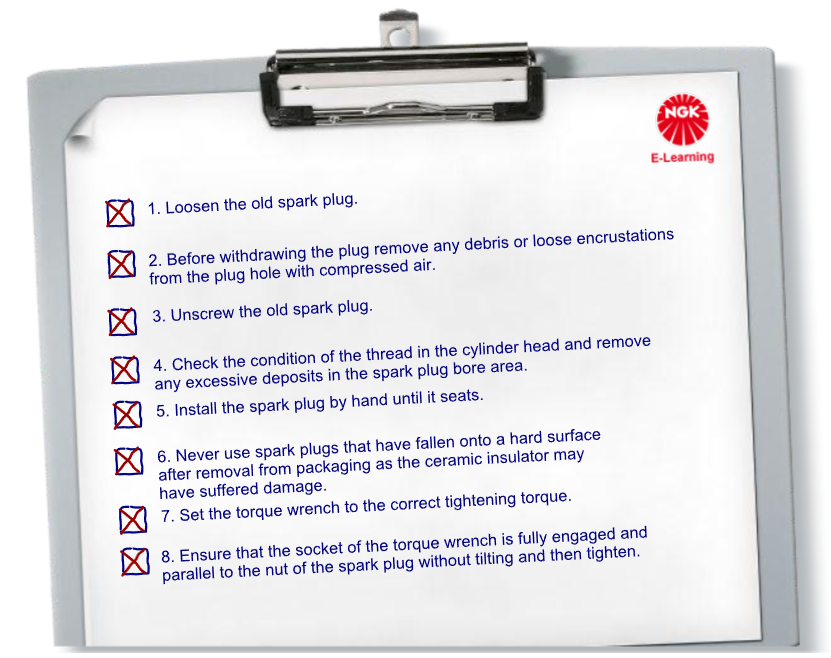
Diagnosis
The firing end appearance
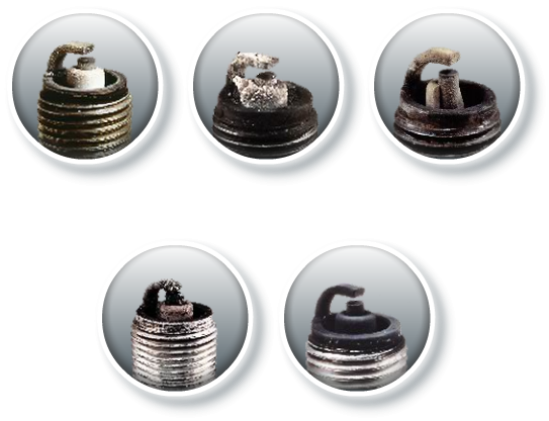
Normal appearance
This is how a spark plug in good condition should look. A white/grey or light brown colour is normal. This colouration is the result of fuel/oil additives which leave residue when burned. This plug condition provides controlled, normal combustion.
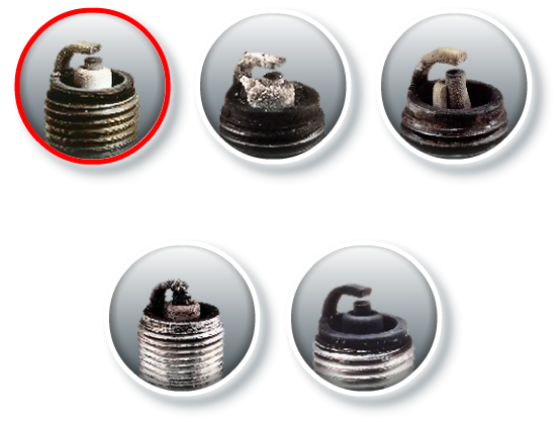
Deposits
Here you can see a spark plug with a heavy accumulation of deposits. This can be caused by poor fuel quality, high oil consumption from a mechanically-worn engine or the burning of coolant from damaged cylinder head seals. This condition can promote uncontrolled ignition as the deposits may start to glow, igniting the air-fuel mixture before the spark occurs.
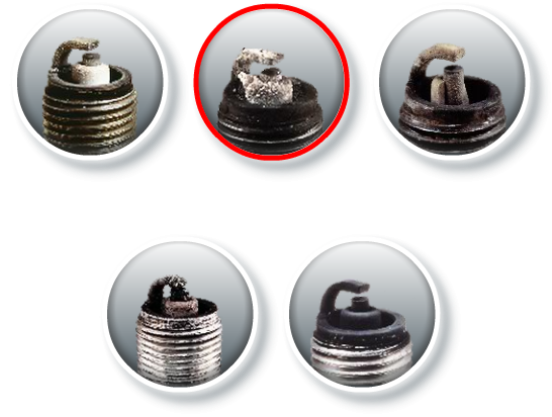
Insulator breakage
A broken insulator, as is visible in this image, can lead to engine damage. The predominant causes of such insulator damage are the use of the incorrect tightening torque, abnormal combustion conditions or the spark plugs were dropped on a hard surface (e.g. workshop floor) before installation.
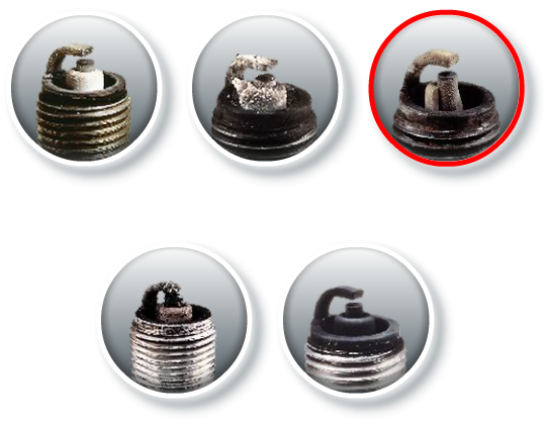
Overheating
The centre and ground electrodes have almost fused together on this spark plug. This can occur if the spark plug becomes severely overheated. In this case, it is also possible that severe engine damage may result due to the formation of local hot spots. Damage to piston crown or valves could result. One cause could be the selection of the wrong spark plug (heat rating) or a malfunction of the engine causing pinking or detonation.
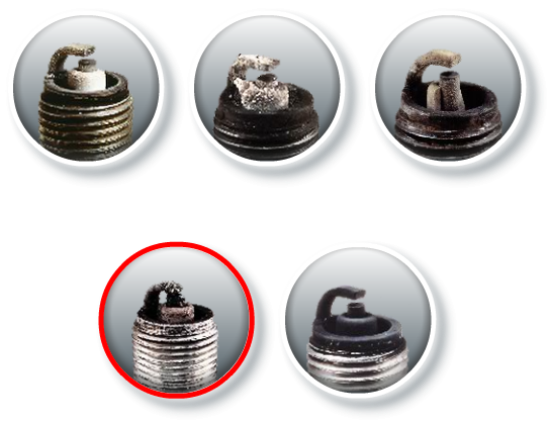
Carbon deposits
Here you can see a spark plug fouled with carbon deposits. Carbon deposits occur if the spark plug is frequently operated below its self-cleaning temperature (450°C) – for example, when only short distances are driven. It could also be that a spark plug with an incorrect heat rating (too cold) was selected or the air-fuel mixture is excessively rich.
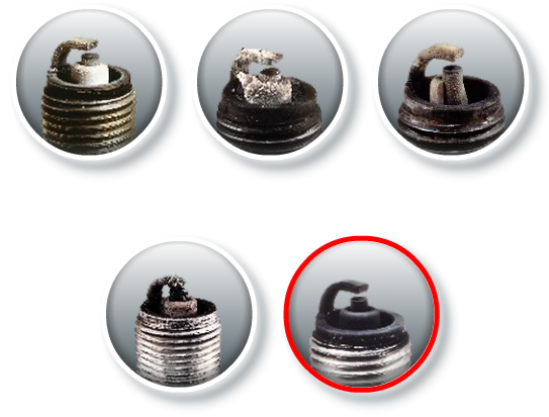
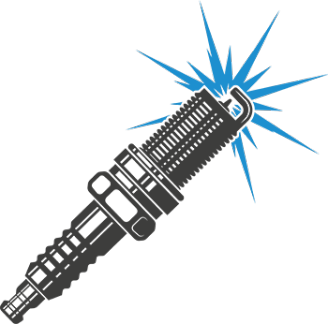