Ignition coils
Principles
The ignition coil’s function within the ignition process
Several components are involved in the ignition of the air-fuel mixture. The spark plug, ignition cables and the ignition coil are all of significant importance. The ignition coil is found at the beginning of the ignition process, as it generates the high voltage which produces the spark discharge at the spark plug.
In the classic type shown here, a mechanical distributor ensures that this voltage reaches the individual cylinders and spark plugs in turn and at the right time.
In this set up, the ignition voltage is fed through the distributor cap and the ignition cable to the spark plug connector. From here, it reaches the end of the centre electrode and crosses the gap to the ground electrode as a spark.
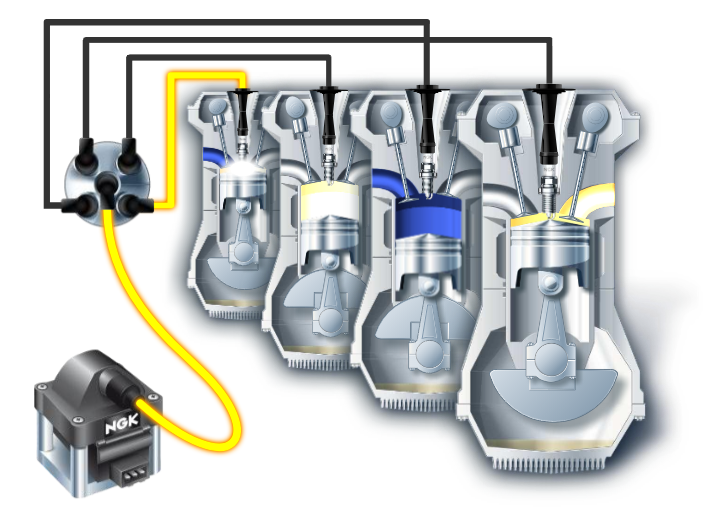
Construction of the ignition coil
The spark plug requires high voltage in order to spark. As the battery generally delivers 12 volts, this output voltage must be transformed. This is the task of the ignition coils. They transform the constant battery voltage into a pulse of many thousands of volts.
As far as the basic principle is concerned, every coil has the same construction: It contains two coils of wire with a common ferromagnetic core.
Both coils are wound with copper wire. The primary coil has relatively few turns of wire with a large wire diameter, while the secondary coil has many more turns of thinner wire. The winding ratio is around 1:150 to 1:200.
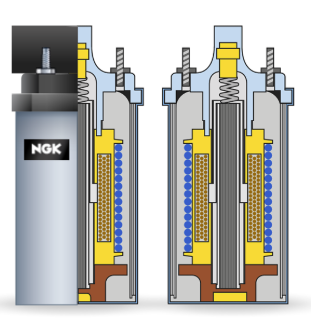
High voltage connection Terminal 4
The high voltage of the secondary electrical circuit is connected to terminal 4 and can be fed to the spark plug via an ignition cable.
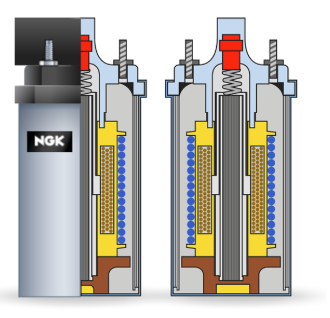
Terminal 15
Terminal 15 forms the connection to the ignition starter switch ('switched positive').
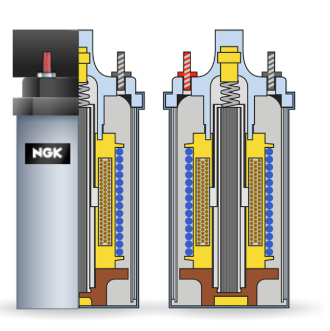
Terminal 1
Depending on the design, this terminal either serves as the connection to the circuit breaker (contact points) or to the ignition unit.
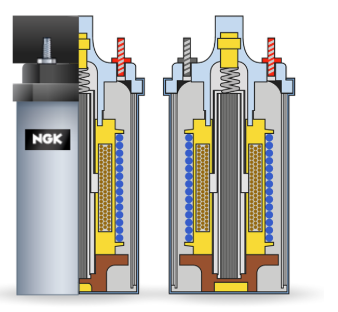
Insulating lid
Like the moulding compound and insulating paper, it ensures optimal insulation of the high voltages produced.
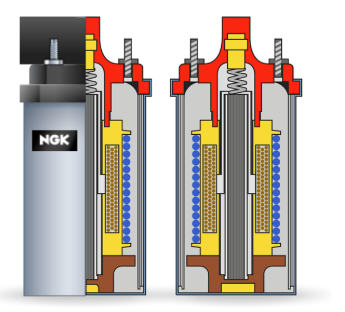
Moulding compound
Like the insulating lid and insulating paper, it ensures optimal insulation of the high voltages produced.
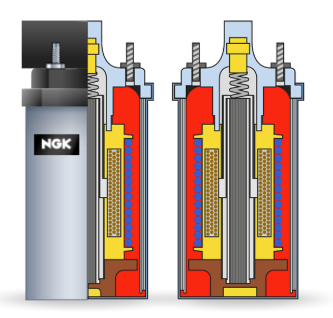
Iron core
The ferromagnetic laminated iron core intensifies the magnetic field produced in the primary coil.
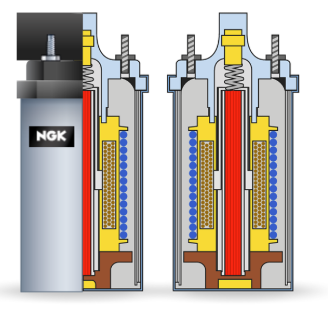
Metal sheet casing
Contributes to closing the magnetic circuit.
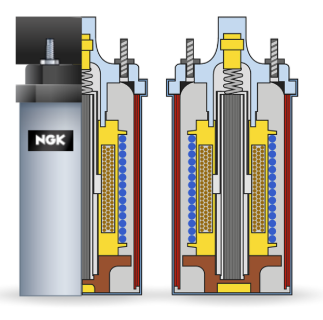
Secondary coil connection
Connects the secondary coil with the high voltage connection, thereby ensuring the transfer of the voltage pulse.
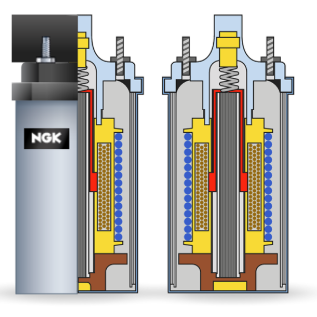
Secondary coil
The secondary coil is wound with many turns of extremely thin wire.
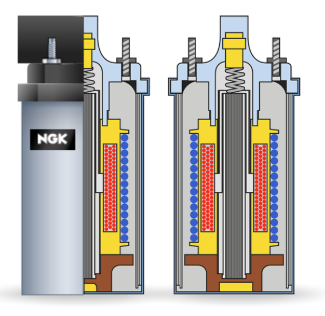
Primary coil
The primary coil is wound with relatively thick wire and has relatively few turns.
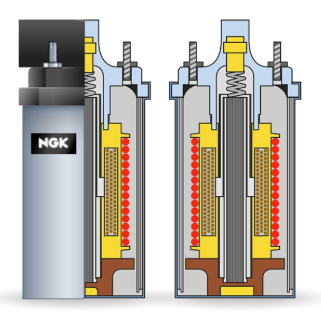
Wound layers of insulating paper
Like the insulating lid and the moulding compound, they ensure optimal insulation of the high voltages produced.
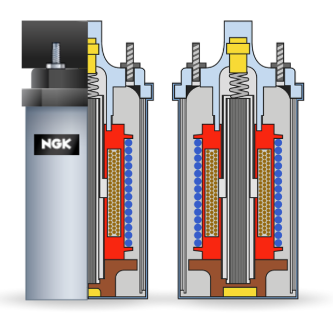
Insulator
Together with the insulating lid, it locates the iron core.
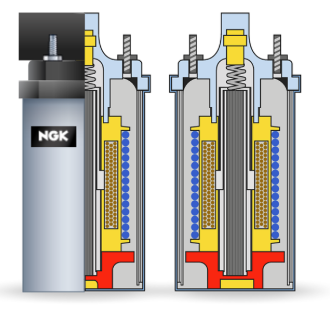
Housing
Robust and produced to the finest tolerances.
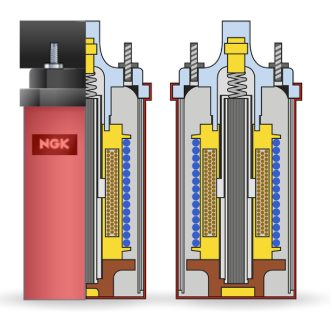
Functional principle of the ignition coil
How does the ignition coil manage to turn 12 volts into 30,000 volts and more? The principle is easily explained:
Terminal 15 of the ignition coil is connected to the positive pole of the battery via the ignition switch. Terminal 1 is connected to ground (earth) via another form of switch. As soon as the electrical circuit is closed, current flows through the primary coil. As with every conductor through which electricity flows, a magnetic field is generated (electromagnetism).
If the electrical circuit is broken, this magnetic field collapses. When this happens, an electrical pulse of 300 to 400 volts is triggered in the primary coil. The collapsing magnetic field of the primary circuit induces a voltage in the secondary circuit as the lines of magnetic flux cut through the many turns of fine wire.
The fact that this induction generates a significantly higher voltage pulse is due to the winding ratio of the primary to the secondary coil. This action is known as transformation.
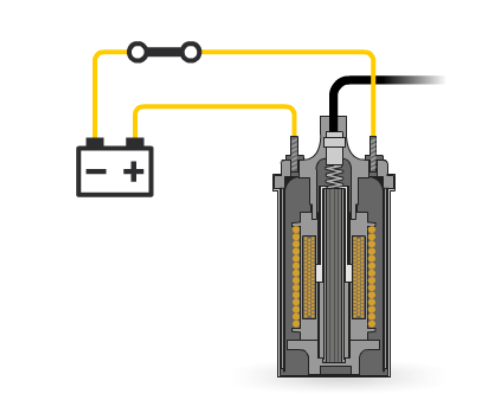
Single spark technology
Ignition coil technology can be split into two fundamental operating principles: "single spark technology" and "dual spark technology".
Single spark ignition coils only release one high voltage pulse via one high voltage output.
The classic form of an ignition coil with single spark technology is the distributor ignition coil: It always releases its ignition energy to the mechanical ignition distributor, which controls distribution to the relevant spark plug in accordance with the firing order.
Today, single spark technology is more popular for automobile manufacturers, but usually in the form of pencil coils. In this case each ignition coil supplies only one cylinder.
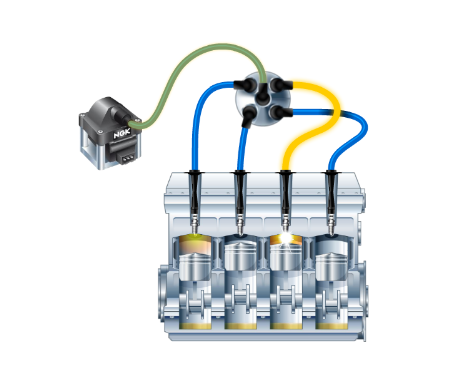
Dual spark technology
Dual spark ignition coils have multiple high voltage outputs which supply two spark plugs with ignition energy simultaneously.
With the classic firing order of a four-cylinder engine, cylinders 1 and 4 as well as cylinders 2 and 3 each receive a high voltage pulse simultaneously.
However, due to the different timing, only one of these cylinders is on the power stroke, during which the air-fuel mixture is ignited.
The other cylinder is on the exhaust stroke. Here, another spark is triggered in order to complete the electrical circuit but this extinguishes with no effect. For this reason, it is known as a "wasted spark".
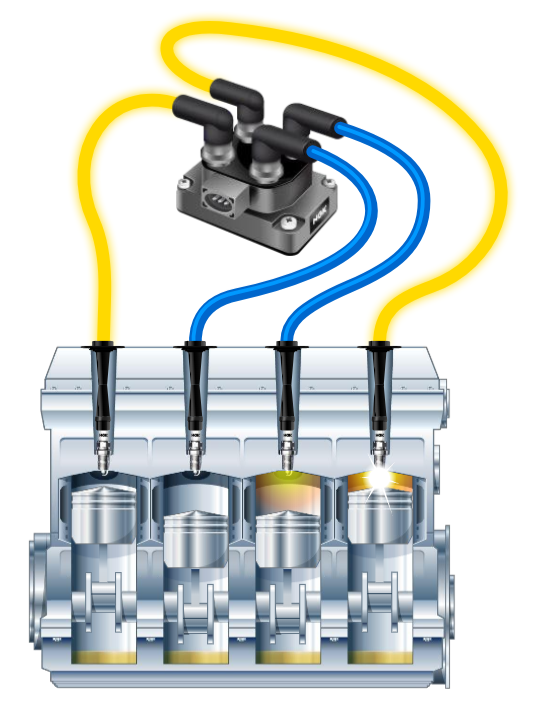
Construction
Evolution of the ignition coil
Many developments have contributed to different types of ignition coils being developed over the years.
Initially, the focus was on preventing failure and improving ignition reliability. However, with the introduction of the 3-way catalytic converter at the beginning of the 1980’s and later, direct fuel injection, the reliability, precise control and specification of different ignition parameters has become increasingly important. This was only possible with electronic systems.
Over the course of the development of modern downsized engines, which fulfil the strict EURO standards and reduce both the production of CO and fuel consumption, the demands grew with regard to ignition voltage requirements, extreme heat resistance, increasing transformation performance, electromagnetic tolerance and weight reduction.
Today, many different types of ignition coil are in use.
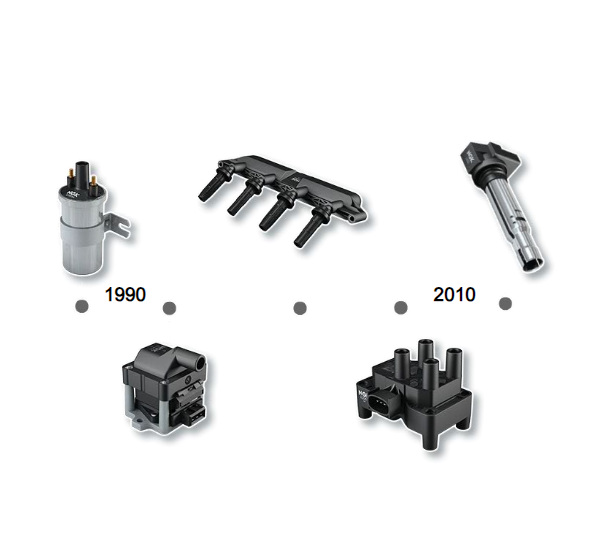
Cylinder coil
The cylinder or 'can' coil is a distributor ignition coil and is one of the oldest types. They can be found in most classic and older vehicles.<br><br>They are usually filled with oil to act as an insulator. The problem: The risk of leakages and short circuits increased over time.

Distributor ignition coil
After the cylinder coil, considerably more compact and powerful versions of the distributor coil were used.<br><br>However, an important weakness of this traditional ignition device remained: the mechanical distribution. Components with moving parts will always be subject to wear and mechanical distributors can also suffer from moisture and contact problems depending on the weather conditions.
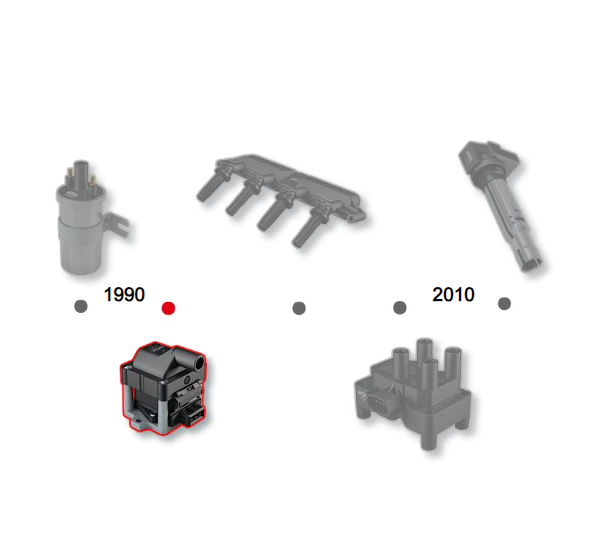
Ignition coil systems
Several automobile manufacturers came up with the idea of combining multiple ignition coils in one complete system.
Such an ignition coil system is known as a 'rail' and, in some applications, can even be equipped with an ionic current measurement device which checks the combustion quality.
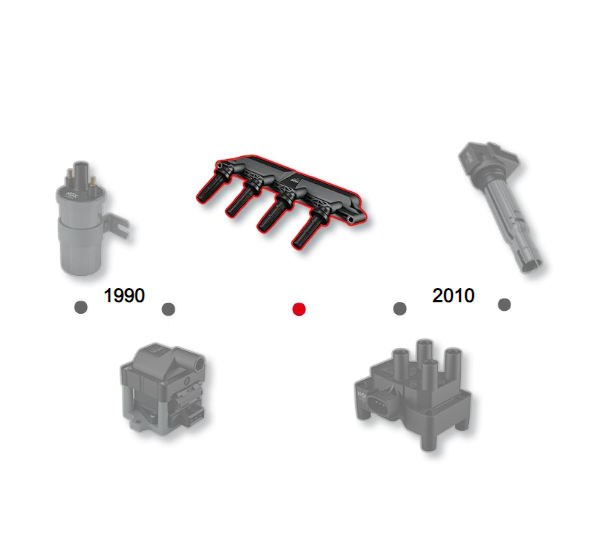
Block coil
Vehicles increasingly had to fulfil new requirements: They were to operate more efficiently, with lower consumption and in a more environmentally friendly manner.
The reliability and control of the ignition plays a special role here. This was achieved with the development of block coils with an integrated ignition module; this is the typical type of coil found on ignition systems with 'static distribution'.
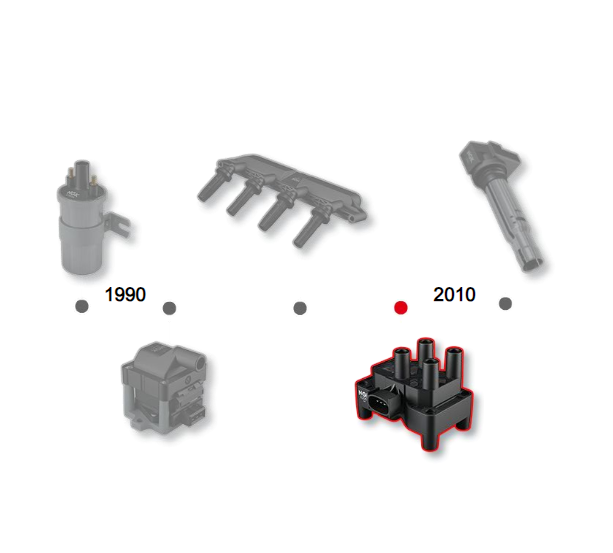
Pencil coils
Since the year 2000 we have seen the major advancement of small downsized engines which, partly thanks to a turbocharger, deliver a similar performance to that of previous, larger engines.
Due to high charging pressure and faster movements of the mixture, they required higher ignition voltages which had to reach the spark plugs with no power loss and without interfering with the on-board electronics.
For this reason, pencil coils were developed which feed the high voltage directly to the spark plug and therefore do not require traditional ignition cables.
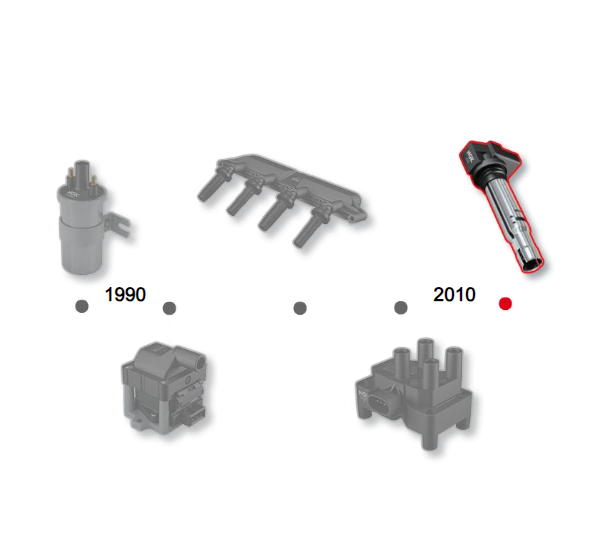
The distributor coil
The distributor coil is the oldest type of coil. It was initially produced in the style of the cylinder coil and filled with oil or asphalt for insulation.
The more modern construction is the block coil with or without integrated amplifier (ignition module). Depending on the vehicle, they can be installed either in the distributor or, more commonly, installed in the engine compartment.
Ignition coils release their high voltage pulse to a rotating distributor. The distributor feeds the pulse via the ignition cables to the respective cylinders, in accordance with the firing order.
The maximum voltage which can be generated by this type of coil is approximately 30,000 volts.
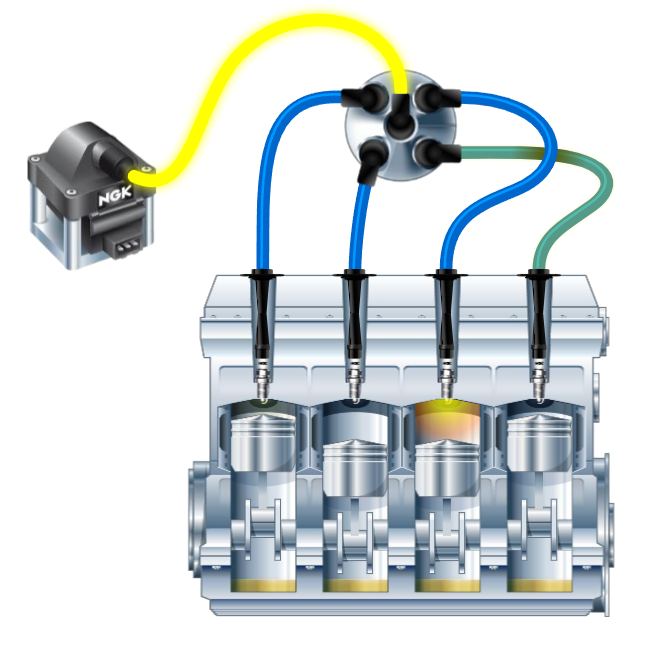
The distributor coil II
Here you can see a diagram of the high voltage distribution using a mechanical distributor.
A rotor arm attached to the top of the distributor shaft rotates underneath the distributor cap. As the distributor rotor passes the contact surfaces of the individual cylinders, the high voltage pulse is fed to the respective cylinders.
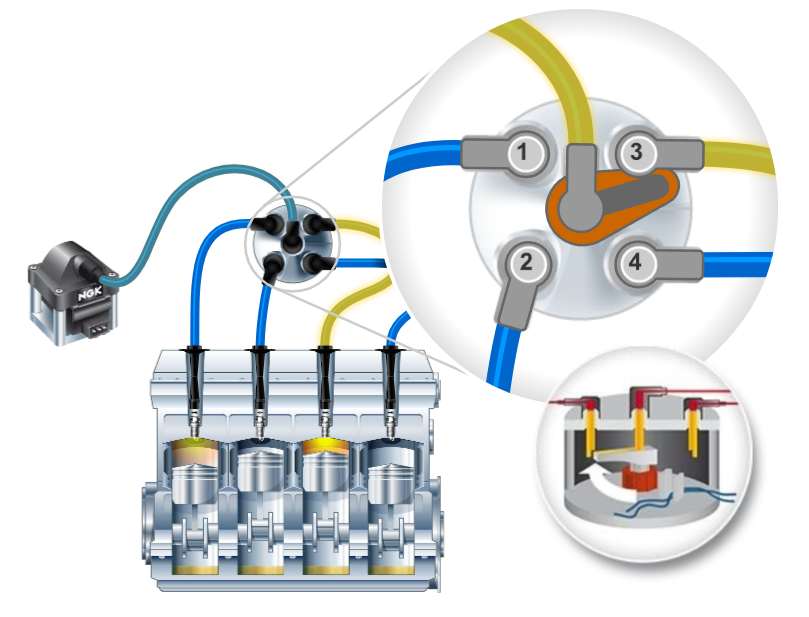
Distributor coil: 360° view
Distributor coil: 360° view
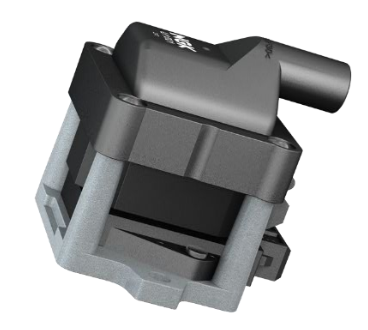
The block coil
In a block coil, multiple ignition coils are combined and supply multiple spark plugs via ignition cables. Most block coils do this using dual spark technology.
Depending on the manufacturer’s requirements, one block coil can therefore supply at least two spark plugs. A block coil with four high voltage outputs and single spark technology, however, can also supply an entire 4-cylinder engine.
Block coils work with static distribution. They are triggered with the help of the ignition module, in order to control the precise timing of the ignition spark. Depending on the vehicle, the ignition module is either part of the engine control system or already integrated into the block coil.
A block coil can generate ignition voltages of up to 36,000 volts.
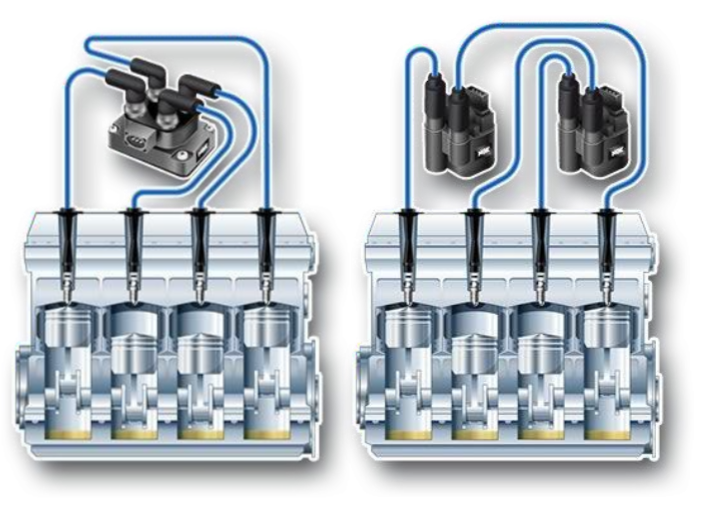
Block coil: construction
Clearly visible in the cross-section here: Two ignition coils which have been integrated into a block coil.
With high quality coils, epoxy resin is poured into the inside of the block coil in a vacuum moulding process: This creates the ideal insulation, as a high density is guaranteed and no air bubbles can be trapped inside.
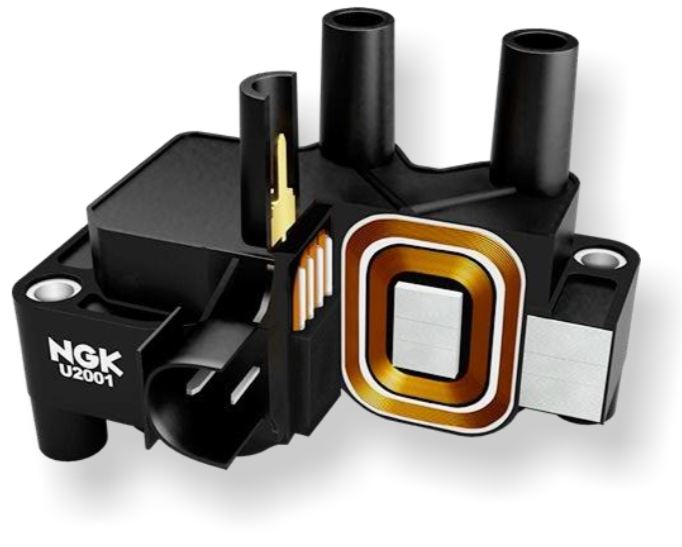
Block coil: 360° view
Block coil: 360° view
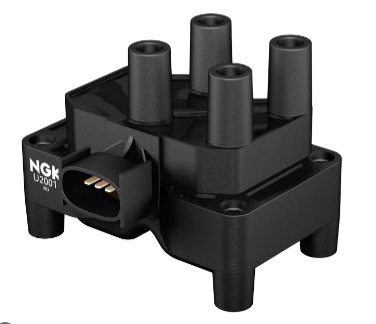
The pencil coil
In modern downsized engines, there is only a limited amount of space available. At the same time, high ignition voltages are required and the sensitive on-board electronics must be protected against electromagnetic interference.
The pencil coil was developed for these requirements. This type of coil is attached directly to the spark plug. It uses the existing spark plug bore in the cylinder head and therefore does not take up any additional space in the engine compartment.
Pencil coils with single spark technology offer one significant advantage: The high voltage is generated extremely close to each spark plug and does not have to be transported via high voltage ignition cables. Potential losses through connections and cables are virtually eliminated.
However, some pencil coils function with dual spark technology whereby only one spark plug is supplied directly, without the need for an ignition cable and a high voltage ignition cable is required for the connection to the second spark plug.
Pencil coils can generate voltages of up to 40,000 volts.
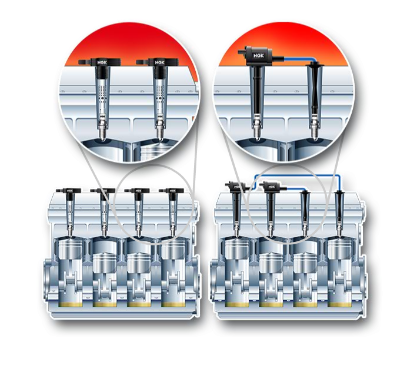
The pencil coil II
Pencil coils can be found in vehicles with fully electronic ignition.
The ignition coil is triggered via the engine control system or via an ignition module integrated into the ignition coil.
In the single spark version, pencil coils have high voltage diodes to prevent the creation of a closing spark.
Dual spark ignition coils do not require this feature and supply two spark plugs with the required voltage simultaneously.
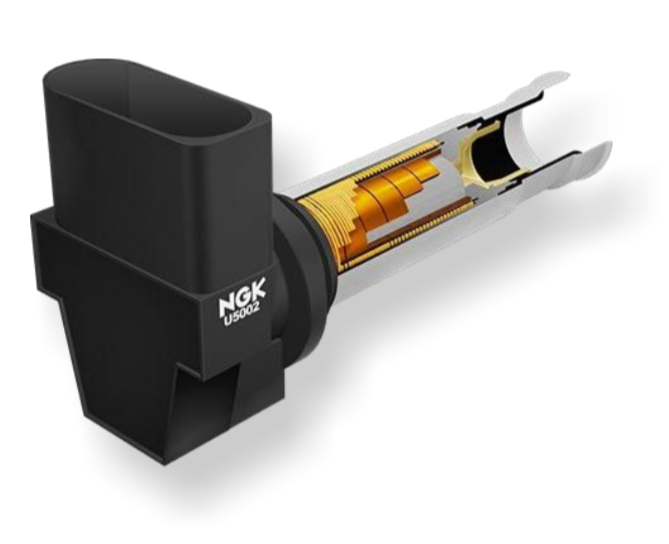
Pencil coil: 360° view
Pencil coil: 360° view
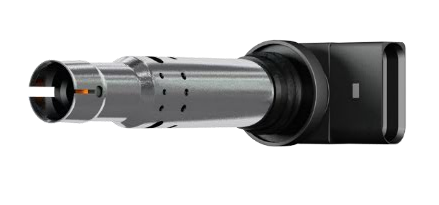
Ignition coil systems
With ignition coil systems, the so-called "rails", multiple pencil coils are often combined in one component.
Like single pencil coils, complete systems are therefore available with single or dual spark technology as well as with or without an ignition module.
In the single spark version, they also require integrated high voltage diodes to prevent undesired pre-ignition due to the closing spark.
Ignition coil systems can generate ignition voltages of up to 40,000 volts.
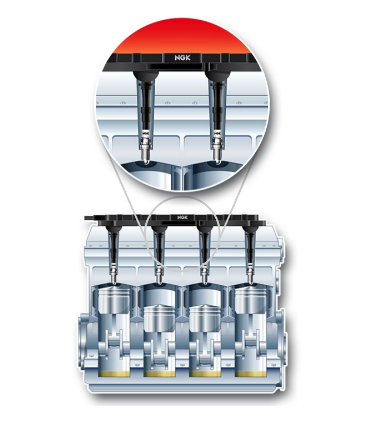
Ignition coil systems II
Here, shown in cross-section: A complete system for a four-cylinder engine. This particular system combines two pencil coils with dual spark technology in one component. Each of the two ignition coils supplies two spark plugs with high voltage via two compression spring contacts.
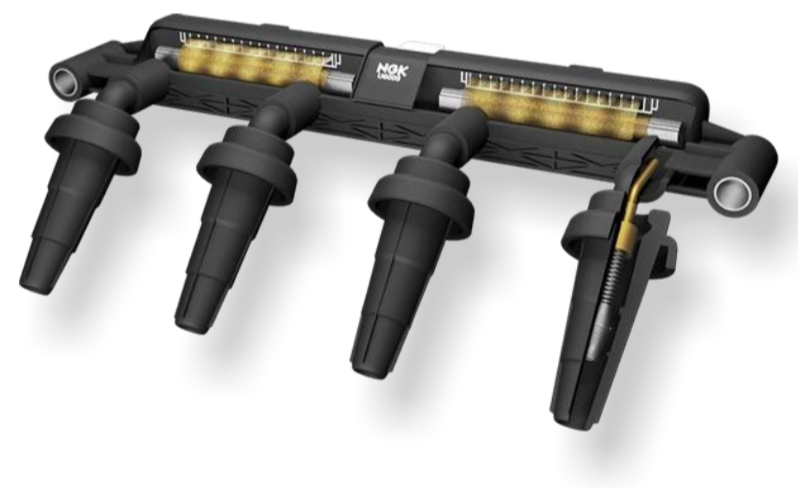
Ignition coil system: 360° view
Ignition coil system: 360° view
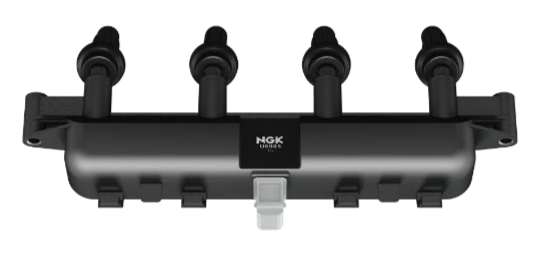
Requirements
Electrical requirements
The demands on the ignition coil in terms of electronic protection are immense. There must be no voltage flashover between the individual turns of wire (so-called inter-turn short circuits), and the high voltage produced must not strike ground. In addition, the electromagnetic field generated by the ignition coil must not interfere with other electronic components and it must be immune to electrical interference from other components itself.
One aspect of coil construction that is extremely important is the moulding or potting compound inside the coil housing. Ideally, it is poured in a vacuum moulding process, so that no air bubbles can become trapped inside. Air is not an ideal electrical insulator and any trapped air bubbles could act as pathways allowing the high voltage to find its way to ground. The quality of the winding itself also plays an important role: The more neatly the wire is wound, the lower the risk of an inter-turn short circuit.
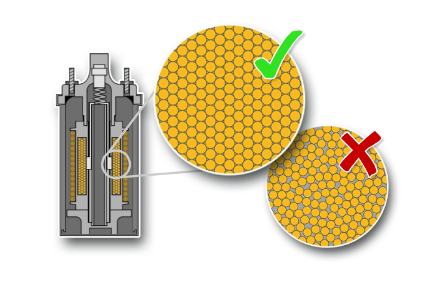
Thermal requirements
Due to the position in which it is necessary to install the ignition coil, it is often exposed to high under bonnet temperatures. This applies in particular to coils which are positioned close to the exhaust tract or to pencil coils, which sit directly on top of the cylinder head.
"Cold shock" also poses a risk: If the hot coil is not sufficiently protected from water splash, it can lead to irreparable damage.
If cold water hits a component which has previously expanded due to heating, it will cool down rapidly and contract. This rapid and uneven cooling can cause stress cracks in the housing or other parts, which can lead to significant problems in operation,
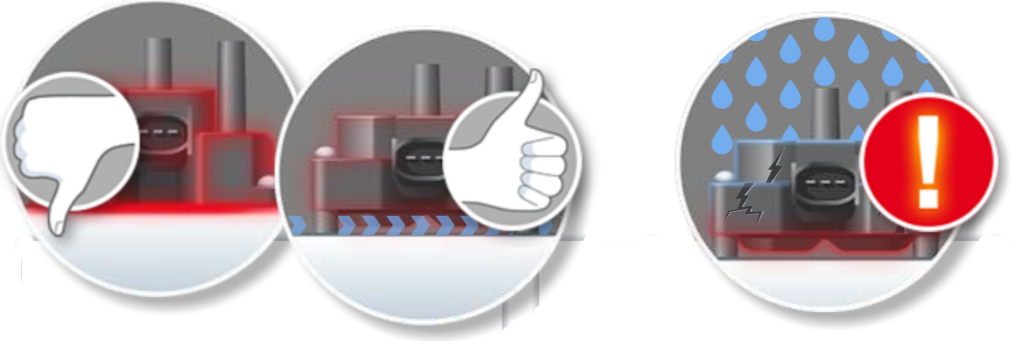
Other design-related requirements
An ignition coil must fulfil many other requirements in order to ensure satisfactory operation.
Firstly, the dimensions must be correct to ensure an accurate mechanical fit. If this is not the case, mechanical stress can occur at the housing which can cause damage and subsequent failure.
Inside the coil and outside on the housing, all materials, components, wiring, welded points and connections must fulfil the highest standards of the automobile industry; from the quality of the plastics used to the exact fit of the seals and the perfect manufacturing of the iron cores.

Installation
Choosing the right ignition coil
The NGK ignition coil range offers the right coil for almost every vehicle in Europe, these coils are divided up into six categories.
NGK’s clever numbering system reveals much about the type and quantity of coils and ignition cables a vehicle may require.
Here you can see the six different categories of NGK ignition coils. They are designated U1 to U6 and this coding represents different ignition coil technologies.
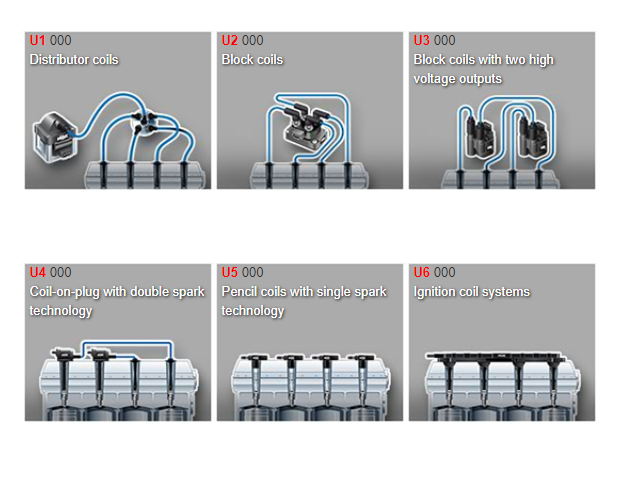
U1 000
An NGK ignition coil in category U1 is almost always for vehicles with a mechanical ignition distributor and it supplies the spark plugs with high voltage via the distributor. Important for vehicle servicing: In this case the number of ignition cables required corresponds to the number of spark plugs. Additionally, a cable from the coil to the distributor is required.
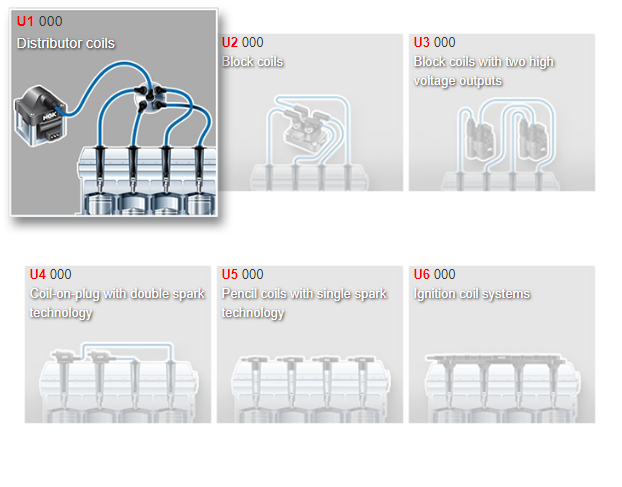
U2 000
The U2 coding describes a block coil with multiple high voltage outputs. A coil like this supplies multiple spark plugs at once. Depending on the vehicle, one or more of these ignition coils would be required. One coil is generally needed per cylinder head. The number of ignition cables corresponds to the number of spark plugs.
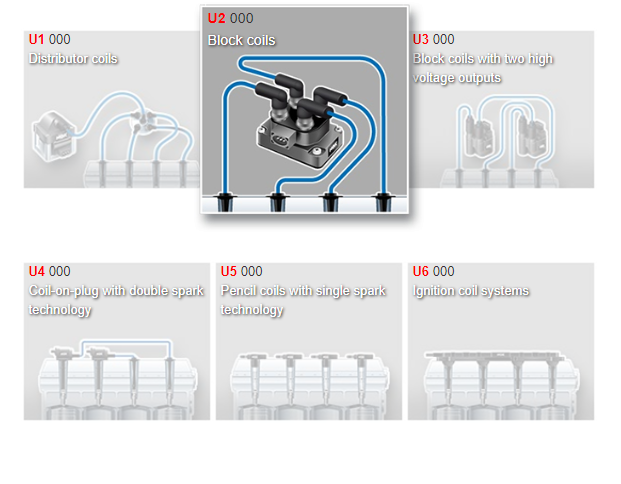
U3 000
Here you can see a block coil with two high voltage outputs. One coil supplies two spark plugs simultaneously with one pulse of energy.
This type has the designation U3 in the NGK numbering system. Depending on the application, several of these coils are required for one vehicle. The number of ignition cables corresponds to the number of spark plugs.
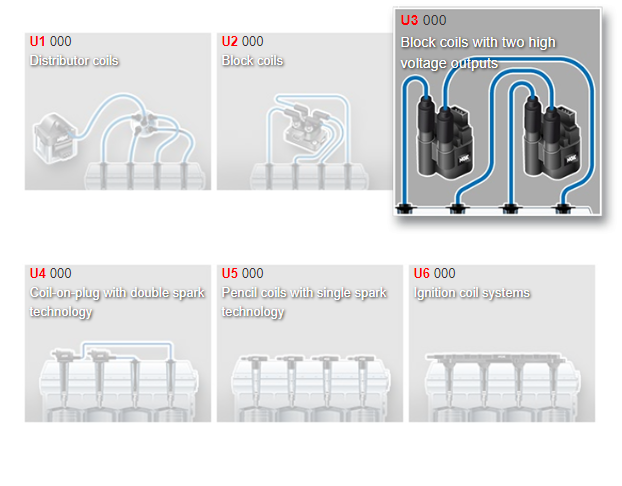
U4 000
This is U4 Coil-on-plug with double spark technology. It is also known as a stick, mushroom or coil on plug design. In this version, called a U4 type, the coil serves two spark plugs with high voltage. The coil is attached directly onto one of the spark plugs and one HT ignition cable is then required per coil to connect to the remaining spark plug.
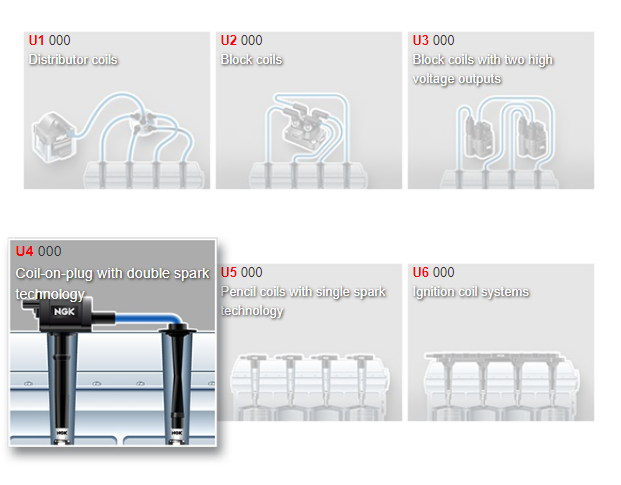
U5 000
Now we come to the pencil coil with single spark technology, again, also known as a stick, mushroom or coil on plug design. These types are identified by the use of U5 coding and only ever supply one spark plug. No ignition cables are required.
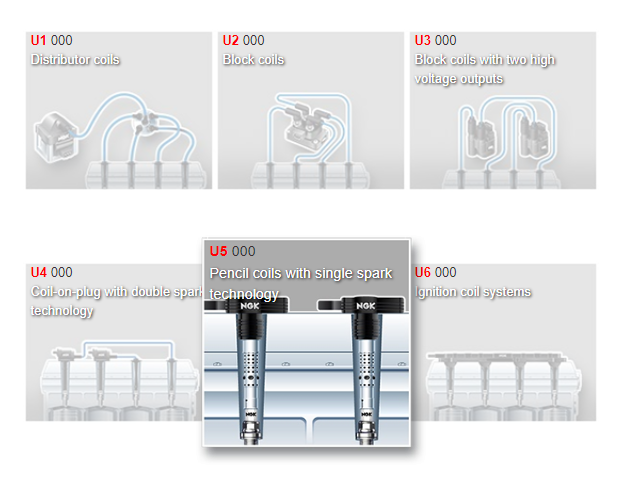
U6 000
The NGK range also includes ignition coil systems, identified by U6. These are cylinder-specific ignition coils in a complete system, so that a group of spark plugs are supplied with high voltage from the same component. In some cases more than one coil system is required per vehicle, for example a V6 configuration may require two. Such a system generally does not require ignition cables.
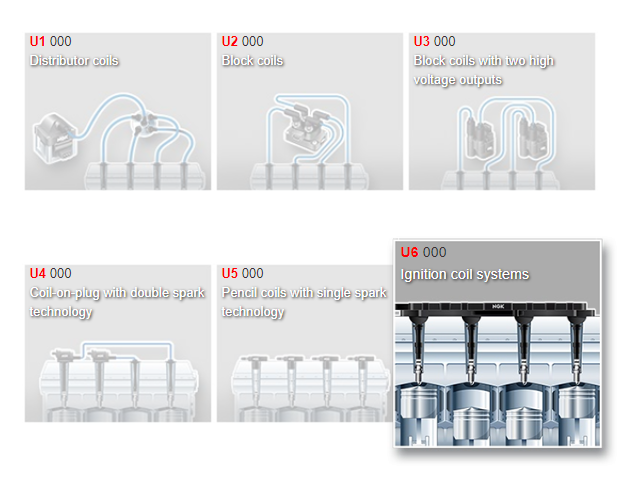
Tips for installation
Correct installation is essential in order to enable the ignition coil to perform its work optimally over its entire service life.
Excessive force must be avoided. If an ignition coil does not fit, the vehicle application should be verified.
The same applies to plug terminals and ignition cables terminals : They must match the respective connections of the ignition coil. If an incorrect connection is used, the contacts will oxidise and become damaged.
The correct tools should always be used; this is especially important when there are specific service tools available. A good example of this is when pencil coils are fitted straight into the spark plug bores. These can be difficult to remove and are at risk of being damaged if a special extractor is not used, enabling straight extraction.
Last but not least, any ignition coil attachment screws should always be tightened to the correct torque.
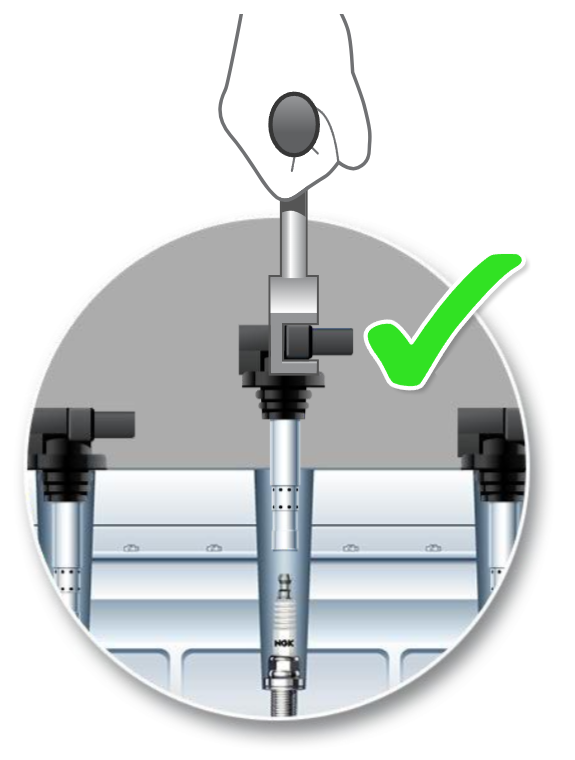
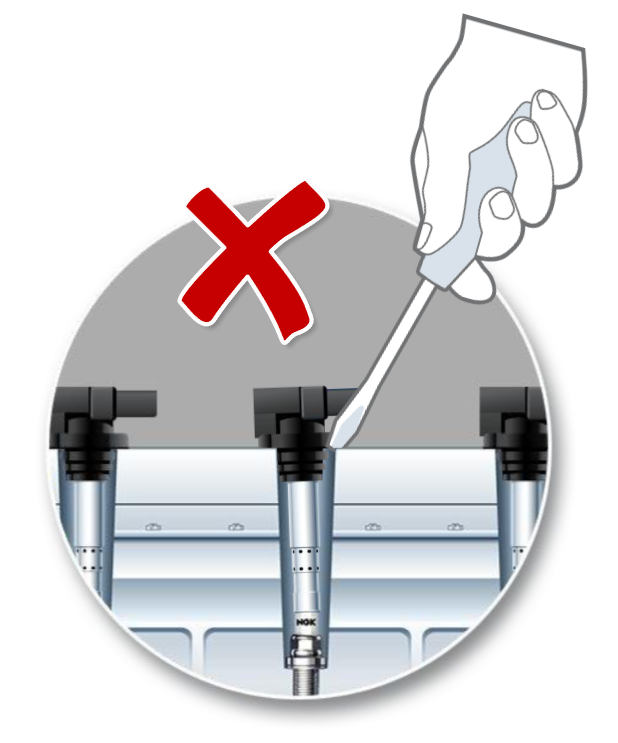
Checklist
The checklist is also available as a PDF download:
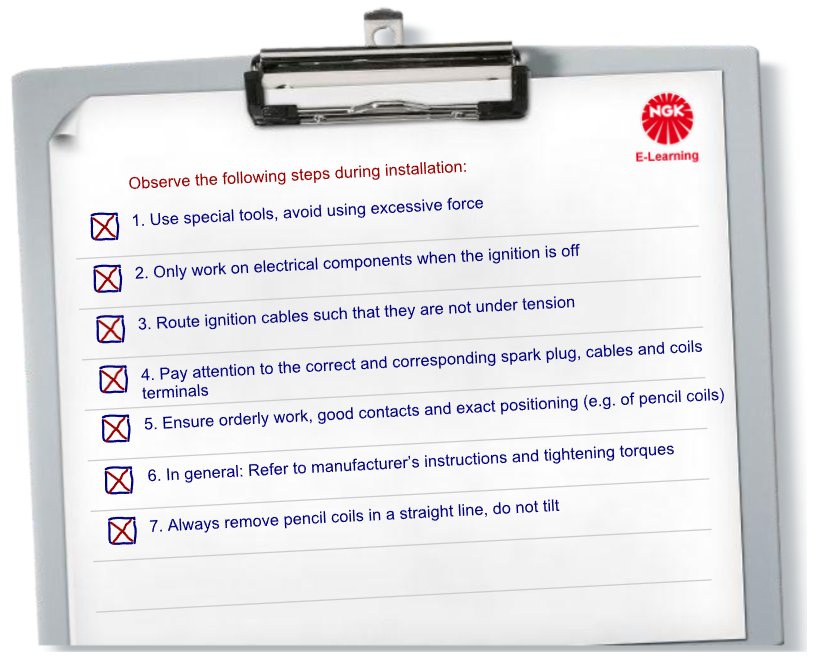
Diagnosis
Measuring resistance at block coils - U2001
The function of a block coil can be tested by checking its electrical resistance with an ohmmeter. The coil is tested while removed. The electrical resistance is measured across the secondary circuit.
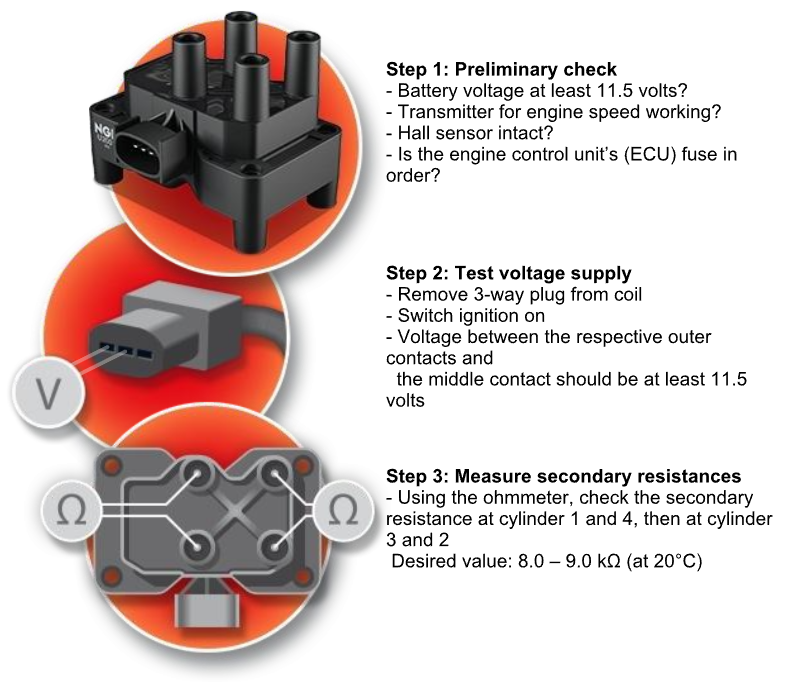
Measuring the magnetic field
As well as measuring the resistance, measuring the magnetic field is a particularly fast and simple way of checking the functionality of the coil.
Because: A functioning ignition coil produces a magnetic field, the strength of which provides information about the functional ability of the coil.
To do this, the detector is held over the electrical component to be checked. An acoustic signal and illuminated LEDs immediately provide information about its functional ability.
How to test an ignition coil with the device:
- Switch the tester on
- Hold the tip of the detector in parallel to and above the area of winding, as described in the instructions
- Read the result at the LED
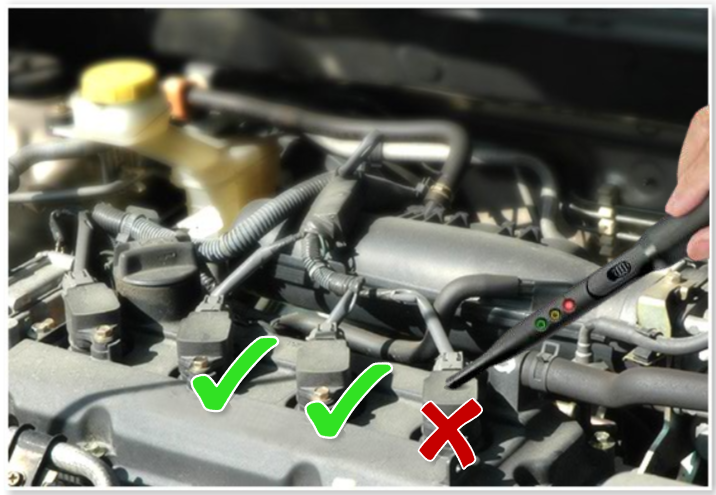