The mass air flow meter (MAF)
The task of the MAF sensor
The Mass Air Flow Sensor (otherwise known as MAF Sensor, Air Mass Meter or Mass Air Flow Meter) is installed between the air filter and the throttle valve and measures the air delivered to the cylinders of the engine. In the case of petrol engines, the intake air mass is the most important value for calculating the required fuel mass. In the case of diesel engines, the measured value in the partial load range is used for controlling the exhaust gas recirculation, while in the full load range for black smoke limitation. The engine control unit (ECU) calculates the maximum injection quantity, which can be burnt without producing smoke.
How the MAF sensor works
The sensor element detects only a part of the entire air mass. In the example shown (Fig.1) there is a channel, the shape of which is intended to minimize the intake air return flow and prevent the deposition of particles on the sensor element. Today's MAF sensors consist of a heating resistor and two temperature sensors (Fig.2). The heating resistor is held by the electronics at a constant temperature of about 160 degrees. The incoming fresh air cools the temperature sensor T1 and is heated by the heating resistor. Therefore a higher temperature is measured at temperature sensor T2. The electronics calculate the air mass from the temperature difference and convert the calculated value into an electrical signal for the ECU.
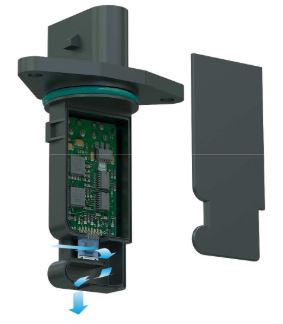
On older air mass meters this is an analogue voltage signal, which is in the range between 0.2 Figure 1: The MAF sensor insert Source: NTK Figure 2: The sensor element of MAF sensor. Source: NTK Page 2 of 8 V and 4.8 V. The signal voltage increases with the air mass. In the case of newer MAF sensors, a digital rectangle signal is sent to the control unit, the frequency of which depends on the changed air mass. The frequency is in the range between 1kHz and 17kHz. On some, as air mass increases the frequency drops. In other types, as air mass increases the frequency increases. Depending on the version, it is possible to record additional measured values for the intake air temperature, the air humidity and pressure in the MAF sensor
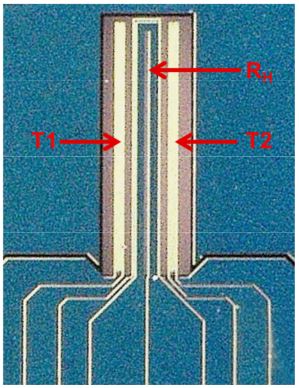
Possible errors and their effects. Electrical failure of MAF sensors
Possible causes are a lack of voltage supply, cable breaks, defective connectors or a failure of the sensor electronics. The ECU detects the fault and stores it in the fault memory. Common error messages are: “ MAF sensor signal implausible, too low or too high”. The ECU attempts to establish emergency running characteristics with substitute values. The values used for this are displayed in the data list of a diagnostic device. The customer complains of judder or loss of performance for example. Before replacing the MAF sensor, check the voltage supply (12 V and/or 5 V) and the cables to the control unit for continuity and short to ground. A circuit diagram is helpful for electrical measurements on the MAF sensor. MAF sensors have between three and six connection pins. The signal pin is frequently found to be the last pin (Fig. 3).
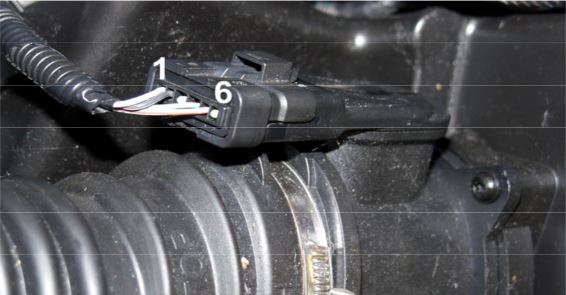
The measurement of the signal voltage
The measurement of the signal voltage serves mainly to check the basic functions of the MAF sensor. For MAF sensors with analogue voltage signals, connect a voltmeter or better an oscilloscope to the pin of the signal voltage and to the signal ground. When the ignition is switched on, the voltage value should be between 0.2 V and 1.0 V, depending on the version. If the voltage is zero volts or 5 V, the air mass meter is defective and must be replaced. When idling, the signal voltage is between 1.5 V and 2 V. On the oscilloscope, you can see a pulsating voltage in the image, which is due to the oscillating air column in the intake manifold (Fig. 4). Upon rapid opening of the throttle the voltage should be above 3.5V. You may reach the highest value of the signal voltage from 4.2 to 4.7 V only when accelerating, under full load, up to nominal speed during a test run. The above mentioned voltage values are standard values. For exact type-specific values, please refer to the documentation provided by the vehicle manufacturer.
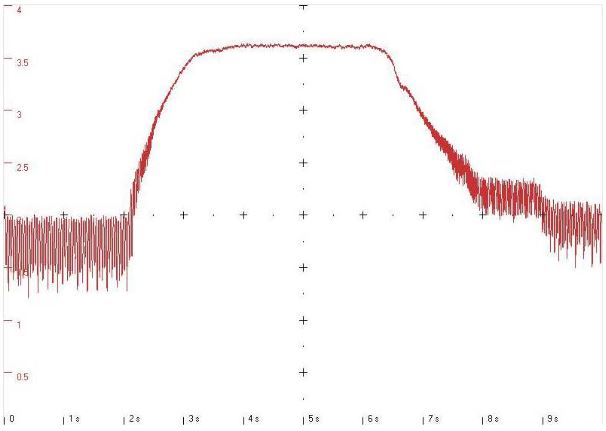
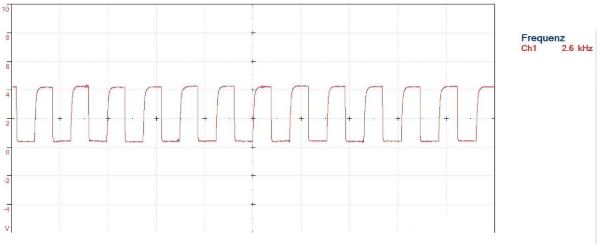
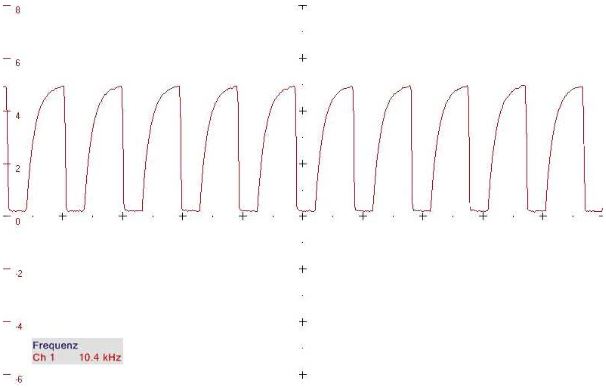
For MAF sensors that produce a square wave signal, you need an oscilloscope or a frequency measuring device. Connect the meter to the signal pin and to the signal ground. When the ignition is switched on, a square-wave signal appears on the oscilloscope, the frequency of which varies between 1 kHz and 15 kHz. (Figures 5 and 6). For MAF sensors with low frequencies of 1 to 2 kHz, the values when opening the throttle must increase (Fig.5). For MAF sensors with high frequency values (with ignition on from 5 to 15 kHz), the frequency must reduce (Fig. 6) In the case of newer air mass meters, not only the air mass but also the intake air temperature is traced as a square wave signal. The signal of the intake air temperature can be seen at the low frequency values (Fig. 7).
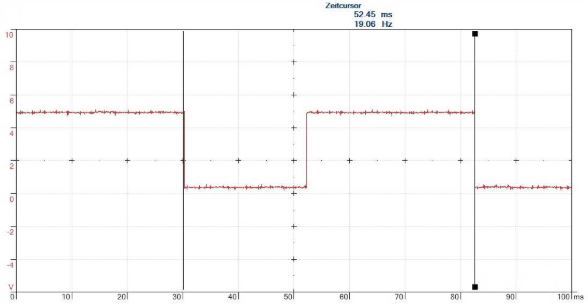
Incorrect measured values of the MAF sensor
When incorrect values are displayed, they are usually below the actual air mass. Frequently the sensor element is polluted by oil vapour from the crankcase ventilation or by particles due to poor air filtration. In the case of petrol engines, the control unit reduces the injection quantity because of the supposed low air mass. The engine judders in the partial load range and does not reach its full power. In the case of diesel engines, the customer complains of a lack of performance because the ECU reduces the injection quantity because of the presumed low air mass. The search for errors is more difficult in this case because the ECU does not store an error or only a subsequent error is in the error memory. In the case of petrol engines, the "mixture too lean, lambda limit reached" error is often indicated. In order to pin point the fault, perform a test drive and record the measured values of engine speed, air mass and the intake manifold pressure in the case of turbo engines. Accelerate, under full load, in a high gear, to reach the rated engine speed. The value of the air mass in grams per second (g/s) for diesel engines should correspond to the engine power indicated in horsepower (Fig. 8),
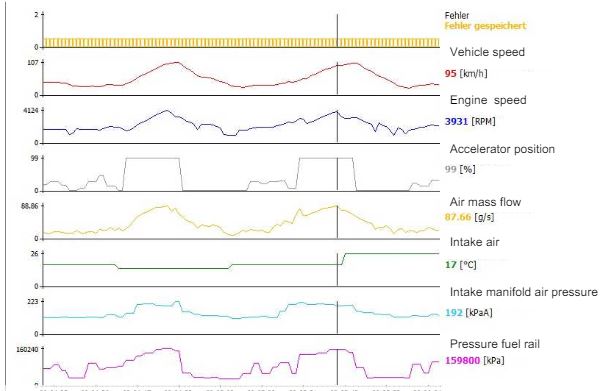
with a petrol engine the engine power in kW (Figs. 9 and 10). These are rough guidelines. For more detailed values, please refer to the vehicle manufacturer's documentation. If the tester does not have access to the factory diagnostics, these values can also be recorded using the EOBD protocol, a diagnostic function with which most vehicles, with an engine from 2000 onwards are equipped. Note: a low air mass value does not clearly indicate a defective air mass meter. Only once all other systems on the air side, i.e. air filter, exhaust gas recirculation, swirl valve, particulate filter and turbocharger are in good order, can you be sure that the MAF sensor is the cause of the fault. A coked intake manifold can also restrict the intake air mass, even though the engine reaches the full charge pressure.
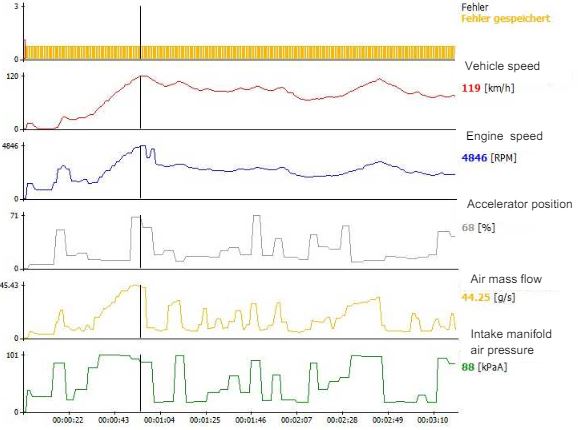
At low air masses, disconnect the MAF sensor connector and perform a brief test ride. If the engine now shows a noticeably higher performance, a defective air mass meter is the probable cause. Cleaning a dirty sensor element is rarely successful. Even if after cleaning a noticeable improvement is found, the measured values offered by a new MAF sensor are not achieved (Fig. 9 and 10). Only the replacement of the defective MAF sensor promises lasting success. Note: In many vehicles engine performance may not be completely recovered immediately. The replacing of the MAF sensor will sometimes require a resetting of the learning values which the vehicle performs during subsequent usage or via scan tool.
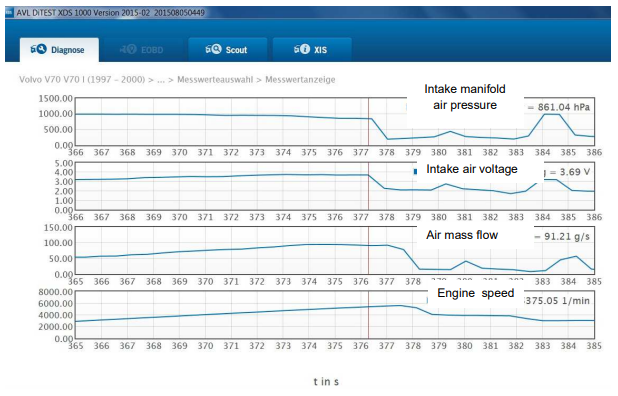