ESPS (Engine Speed & Position Sensor)
Grundlagen
Was messen sie?
Funktion/Aufgabe
Diese Sensoren liefern Informationen über die genaue Position und die Geschwindigkeit verschiedener Motorteile.
Geschwindigkeit:
- Kurbelwelle
Position:
- Kolben
- Nockenwelle
- Ventile
Aufgaben
- Um die Kraftstoffeinspritzung und Zündung in allen Betriebszuständen des Motors sicherzustellen, muss das Motorsteuergerät (ECU) Informationen über die Motordrehzahl und -position erhalten.
- Zur Bestimmung der Motordrehzahl wird das Kurbelwellensignal verwendet. Darüber hinaus liefert es die Information, wann sich der erste Zylinder im oberen Totpunkt befindet.
- Der Nockenwellensensor gibt Auskunft darüber, in welchem Takt sich die einzelnen Zylinder befinden.
- Anhand beider Signale kann das Motorsteuergerät (ECU) nun regeln, wann der Kraftstoff eingespritzt und wann das Kraftstoff-Luft-Gemisch von den Zündkerzen gezündet wird.
- Wenn der Nockenwellensensor ausfällt, kann das Motorsteuergerät (ECU) aus dem Signal des Kurbelwellensensors ein Notprogramm fahren.
- Sollte der Kurbelwellensensor ausfallen, reichen die Informationen des Nockenwellensensors nicht aus, um den Motor am Laufen zu halten.
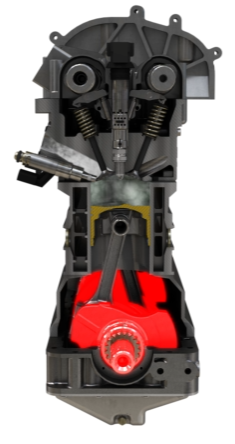
Kurbelwellensensor (Drehzahl)
Funktion/Aufgabe des Kurbelwellensensor (Drehzahl)
- Der Kurbelwellensensor misst die Drehzahl und Position der Kurbelwelle.
- Dies sind wichtige Informationen, die das Motorsteuergerät (ECU) benötigt, um arbeiten zu können.
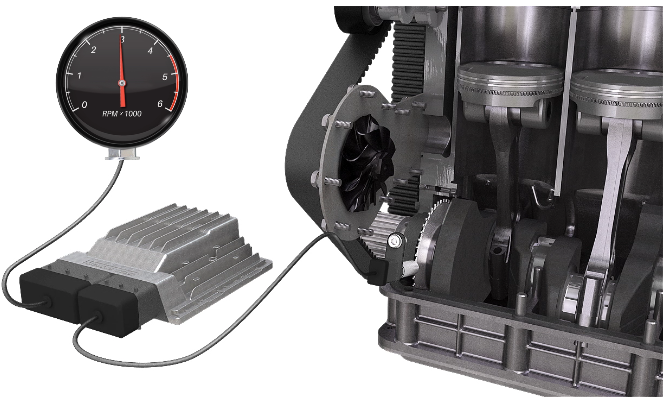
Nockenwellensensor (Position)
Funktion/Aufgabe vom Nockenwellensensor (Position)
Der Nockenwellensensor misst die Position der Nockenwelle. Anhand dieses Signals wird - in Verbindung mit der Kurbelwellenposition - ermittelt, in welchem Hub sich die einzelnen Zylinder befinden. Die ECU benötigt das Signal, um zu bestimmen, wann Kraftstoff eingespritzt und die Zündkerze zündet.
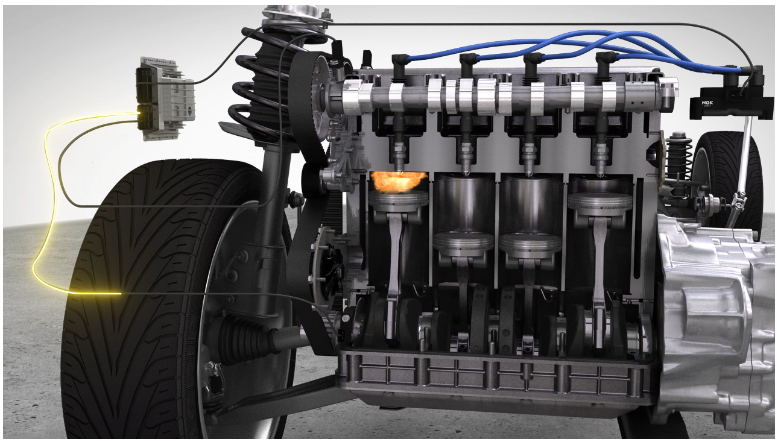
Kurbelwellensensoren
Geschichte/Entwicklung der Kurbelwellensensoren
Wird für Benzin- und Dieselmotoren mit elektronischen Einspritzsystemen verwendet. Benziner: ab den 80er Jahren ("Motronic" 1979); ab ~ 1990 haben fast alle Fahrzeuge Kurbelwellensensoren.
Diesel: Beginn mit der "Common-Rail"-Technologie 1997 (Alfa 156 JTD).
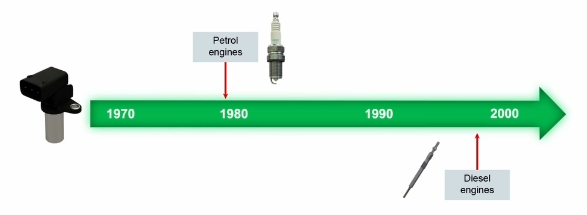
Nockenwellensensoren
Geschichte/Entwicklung von Nockenwellensensoren
- Wird für Benzin- und Dieselmotoren mit elektronischen Einspritzsystemen verwendet.
- Viele neuere Motoren haben zwei Nockenwellen und oft zwei Nockenwellensensoren.
- Bei der variablen Nockenwellensteuerung werden die Sensoren auch zur Überwachung dieser Funktion eingesetzt.
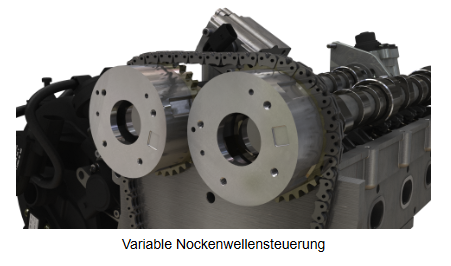

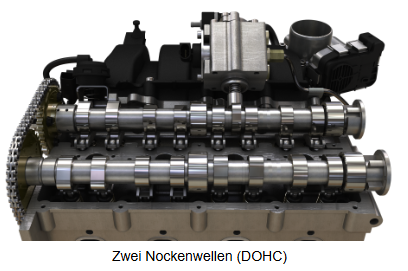
Aussehen - Kurbelwellensensoren
Geschichte/Entwicklung
Verschiedene Ausführungen von Kurbelwellensensoren
Die wichtigsten Unterschiede:
- 2 oder 3 Pins
- Mit oder ohne Kabel
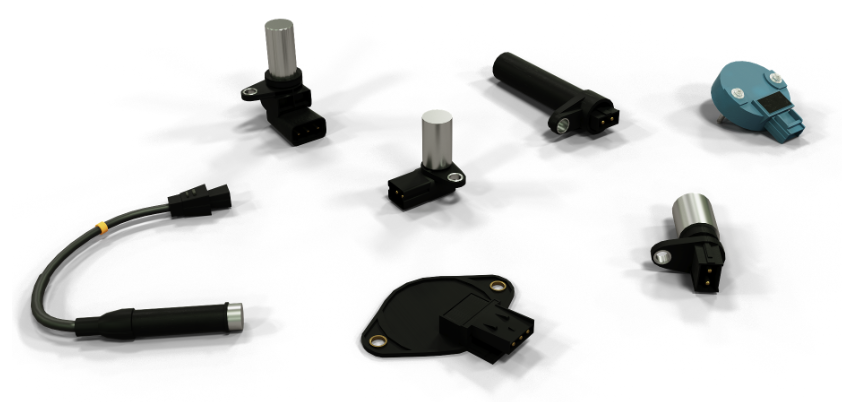
Aussehen - Nockenwellensensoren
Geschichte/Entwicklung
Verschiedene Ausführungen von Nockenwellensensoren
Hauptmerkmale:
- Meistens 3 Pins
- Mit oder ohne Kabel
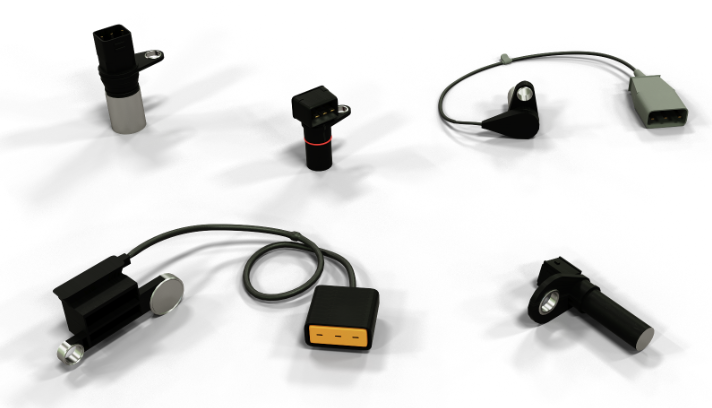
Einbaulage - Kurbelwellensensoren(Drehzahl)
- Der Kurbelwellensensor befindet sich in der Nähe der Kurbelwelle.
- Er nimmt das Signal eines Zahnrads oder einer Scheibe auf, die sich mit der Kurbelwelle dreht.
- Der Sensor kann sich auf einer der beiden Seiten (Antriebsriemen- oder Schwungradseite) der Kurbelwelle oder in der Mitte befinden.
- In einigen Fällen hat der Sensor Kontakt mit dem Motoröl.
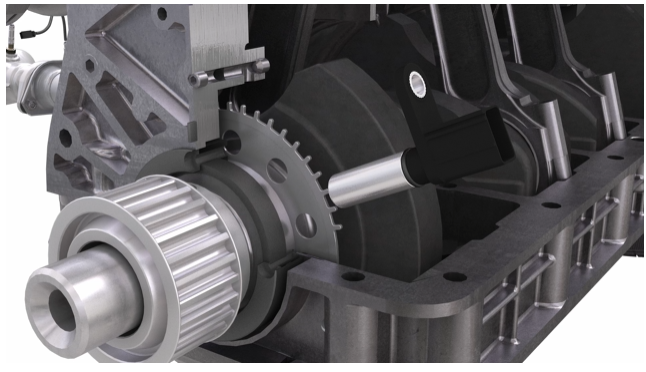
Einbaulage Nockenwellensensor (Position)
Position der Nockenwelle:
Die Position der Nockenwelle ist (zusammen mit der Position der Kurbelwelle) ein Indikator für die Position des Kolbens und ermöglicht es dem Steuergerät zu bestimmen, in welchem Hub sich jeder Kolben befindet.
Der/die Nockenwellensensor(en) ist/sind in der Nähe der Nockenwelle(n), im oder in der Nähe des Zylinderkopfes verbaut.
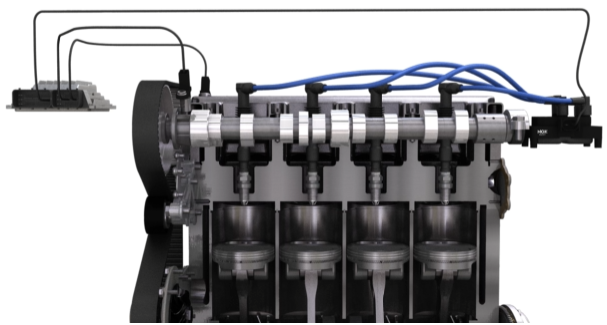
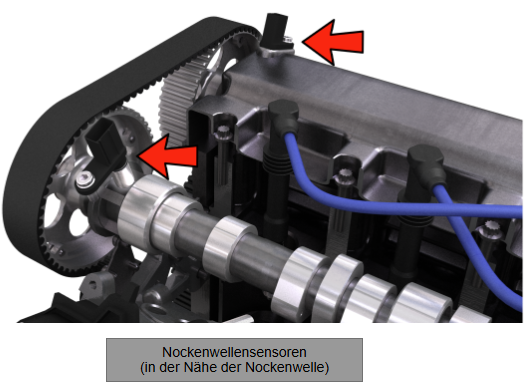
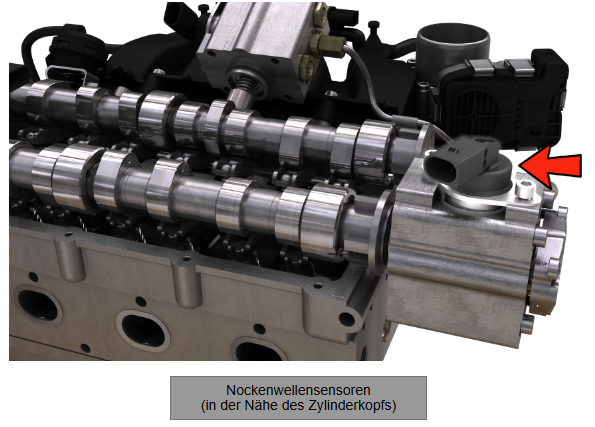
Aufbau
Funktionsprinzip
- Die Sensoren arbeiten entweder nach dem induktiven Prinzip oder nach dem Hall-Effekt-Prinzip.
- Sie können nicht untereinander ausgetauscht werden.
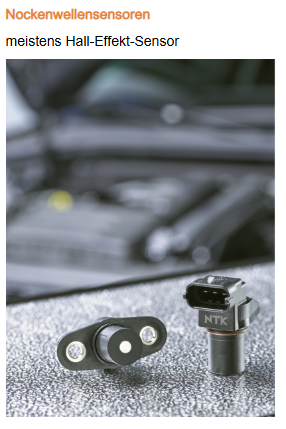

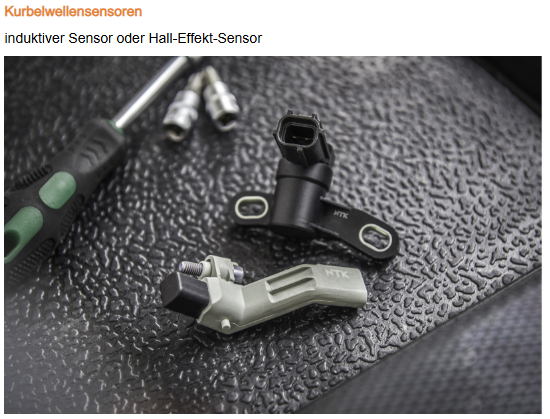
Prinzip der Induktion
Elektromagnetische Induktion ist das Auftreten einer elektrischen Spannung entlang einer Leiterschleife (z. B. einer Spule) aufgrund einer Änderung des magnetischen Flusses.
Das Induktionsprinzip lässt sich anhand eines einfachen Experiments leicht veranschaulichen.
Eine Spule wird an ein empfindliches Voltmeter angeschlossen, dann wird ein Magnet durch die Spule bewegt. Die Bewegung erzeugt eine elektrische Spannung, weil sich der magnetische Fluss ändert. Während der Bewegung des Magneten kann eine Spannung gemessen werden. Je schneller die Bewegung, desto höher die gemessene Spannung.
Die erzeugte Spannung ist jedoch sehr niedrig. Um diesen Effekt zu verstärken, wird die Spule um einen Eisenkern gewickelt. Der Eisenkern verstärkt das Magnetfeld, weil sich die Elementarmagnete (die Atome in seinem Metallgitter) entsprechend dem Magnetfeld ausrichten.
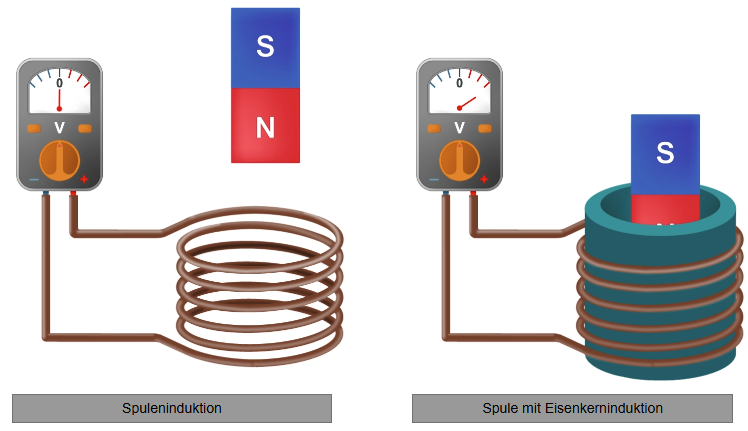
Induktiver Sensor
Der Sensor besteht aus einer Spule, in deren Mitte sich ein Eisenkern befindet. Darunter befindet sich ein Magnet, der ein Magnetfeld erzeugt.
Durch seine Einbaulage ist der Sensor so ausgerichtet, dass das Magnetfeld des Magneten durch das Zahnrad der Kurbelwelle beeinflusst werden kann.
Wenn sich das Rad zu drehen beginnt, bewegt sich das Magnetfeld auf und ab und erzeugt eine elektrische Spannung in der Spule.
Je schneller sich das Rad dreht, desto höher ist die erzeugte Spannung.
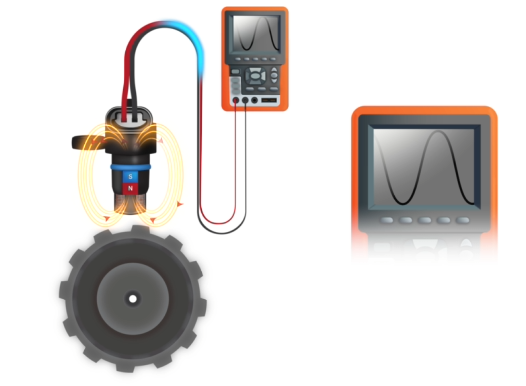
Hall-Effekt-Prinzip
Der Halleffekt tritt auf, wenn ein stromdurchflossener Leiter durch ein Magnetfeld beeinflusst wird. Das Magnetfeld beeinflusst die Elektronen, die sich durch den elektrischen Leiter bewegen. Sie bewegt die Elektronen senkrecht zur Stromflussrichtung und zur Richtung des Magnetfelds. Daraus ergibt sich eine Spannung, die senkrecht zum Stromfluss gemessen werden kann.

Hall-Effekt-Sensor
Der Sensor besteht aus einem elektrischen Leiter, der von der ECU entweder mit 5V oder 12V Spannung versorgt wird. Wirkt ein Magnetfeld auf den stromdurchflossenen Leiter, wirkt die Lorentzkraft auf die Elektronen. Dies führt zu einem Überschuss an Elektronen auf der einen und einem Mangel an Elektronen auf der anderen Seite. Die Ladungsdifferenz kann in Form einer Spannung gemessen werden und wird über die Signalleitung an das Steuergerät übertragen. Das vereinfachte Schema zeigt den Stromfluss mit und ohne den Einfluss des Magnetfeldes.
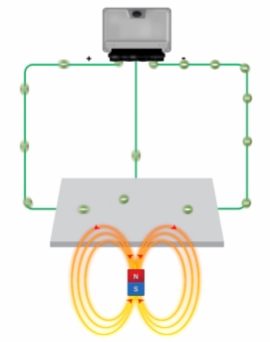
Hall-Effekt-Sensor
Wird nun das Magnetfeld durch ein Zahnrad abwechselnd zum Sensor und wieder weg bewegt, wird ein quadratisches Ausgangssignal von 0 bis 5V oder 12V erzeugt.
Je schneller sich das Rad dreht, desto kürzer ist die Zeitspanne zwischen hohem und niedrigem Niveau.
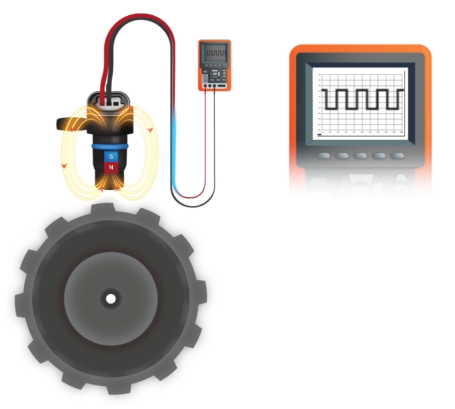
Kurbelwellendrehzahl und Positionserkennung
- Durch einen "Trick" kann die ECU die Kurbelwellendrehzahl und die Kurbelwellenposition gleichzeitig erkennen.
- Das Zahnrad hat einen größeren Spalt an einer bestimmten Stelle.
- Das vom Sensor erzeugte Signal spiegelt diese große Lücke wider, und so kann das Steuergerät die Position berechnen.
- Dieses Merkmal im Signal wird als Referenzmarke bezeichnet. Bei induktiven Sensoren tritt an diesem Punkt eine größere Spannungsspitze auf als im restlichen Signal. Bei Hall-Effekt-Sensoren tritt an diesem Punkt eine etwas längere Hochpegelperiode auf.
Animation zur Kurbelwellendrehzahl und Positionserkennung anschauen
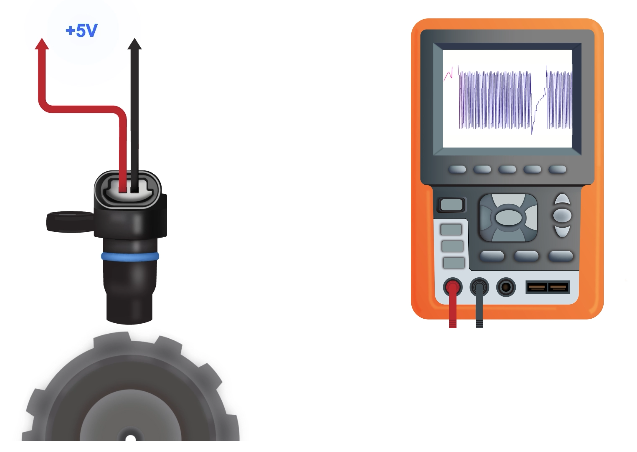
Vergleich Hall-Effekt-Sensor und induktiver Sensor
Hall-Effekt-Sensor | Induktiver Sensor |
---|---|
Integrierte Elektronik | Nicht-Integrierte Elektronik |
Externe Stromversorgung 5V | Erzeugt ein Signal, keine externe Stromversorgung |
Quadratisches Ausgangssignal (0V/5V) | Wellenförmiges Ausgangssignal |
Die Spannung steigt nicht mit der Radgeschwindigkeit | Die Spannung steigt mit der Radgeschwindigkeit und hängt vom Abstand zum Rad ab |
3 Pins | 2 oder 3 Pins |
Geschwindigkeitserkennung bei nahezu Stillstand (Erkennung niedriger Geschwindigkeit) | Geschwindigkeitserfassung erst ab einer bestimmten Geschwindigkeit möglich. |
Das Design des Sensors ist kleiner und leichter | Das Design des Sensors ist größer |
Die Empfindlichkeit gegenüber elektromagnetischen Störungen ist geringer | Die Empfindlichkeit gegenüber elektromagnetischen Störungen ist höher |
Änderungen im Luftspalt zwischen Sensor und Zahnrad haben keinen direkten Einfluss auf das Signal | Änderungen im Luftspalt zwischen Sensor und Zahnrad haben einen direkten Einfluss auf das Signal |
Höhere Resistenz gegen Vibrationen und Temperaturschwankungen | Niedrigere Resistenz gegen Vibrationen und Temperaturschwankungen |
Einbau
Einbau
- Nach dem Einbau neuer Nocken- und Kurbelwellensensoren ist bei vielen Fahrzeugen ein "Lernverfahren" erforderlich. Hierfür ist ein Scan-Tool erforderlich.
- Das Motorsteuergerät (ECU) "lernt" die genaue Position des Sensors.
Hintergrund: Die Hallsensorelemente im Sensorgehäuse befinden sich nicht unbedingt an der gleichen Position wie beim alten Sensor. Dies führt dazu, dass das Signal etwas später oder früher kommt.
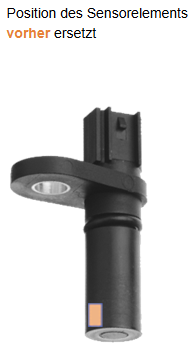

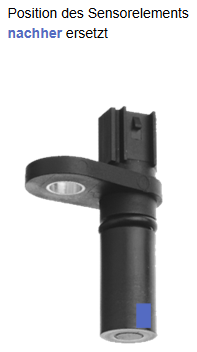
Diagnose
Folgen von Sensorausfällen
Nockenwelle
- Ohne dieses Signal kann die ECU (bei den meisten Fahrzeugen) den Motor weiterlaufen lassen.
- Der Motor startet verzögert. Der Motor läuft im Notprogramm. Die Motorkontrollleuchte leuchtet auf.
- Die variable Nockenwellensteuerung (sofern der Motor über diese Funktion verfügt) funktioniert nicht.
Kurbelwelle
- Ohne dieses Signal (Haupteingangssignal für die ECU) kann die ECU den Motor nicht am Laufen halten.
- Der Motor läuft nicht und springt nicht an.
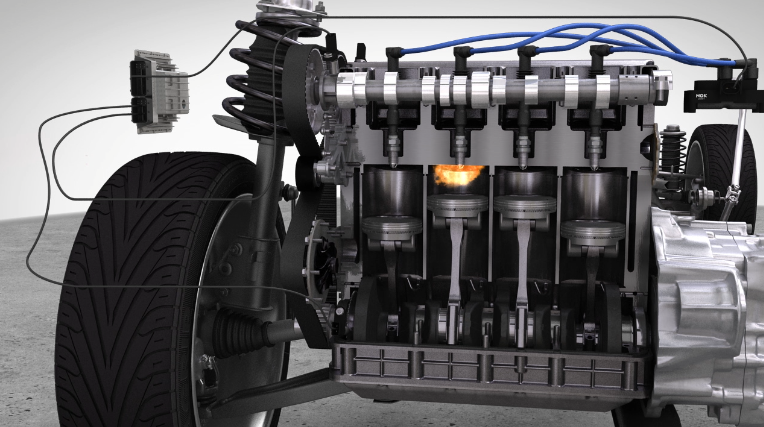
Symptome eines defekten Kurbelwellensensors
- In den meisten Fällen läuft der Motor nicht und ein DFC (Diagnosefehlercode) wird gespeichert.
- Manchmal tritt der Fehler nur sporadisch auf. Die folgenden Symptome deuten auf einen defekten Kurbelwellensensor hin:
- Schlechter Start
- Ruckelnder Motor
- Schlechte Leistung
- Zündaussetzer
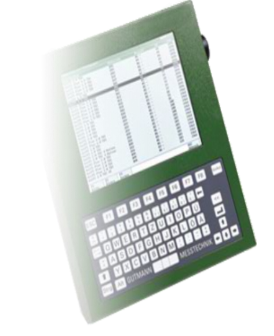
Korrodierte Kontakte
In diesem Fall ist Wasser in das Steckergehäuse eingedrungen und hat zu Korrosion an den Kontakten geführt. Wenn der Sensor ausgetauscht wird, sollten die Dichtungen des Steckers, die Kontakte des Steckers und die Drähte zwischen dem Stecker und dem Motorsteuergerät sorgfältig überprüft werden.
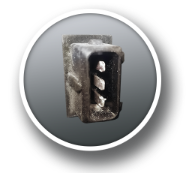
Gebrochene/beschädigte Kabel
Die Kabel sind durch äußere Einwirkung beschädigt worden. Dies kann durch eine starke Zugbewegung (zu stramm verlegtes Kabel, Ziehen am Kabel bei der Montage) oder durch rotierende Teile (Kabel reibt an rotierenden Teilen, z.B. Kurbelwellenrad) verursacht werden. Achten Sie deshalb bei der Installation auf die richtige Kabelführung.
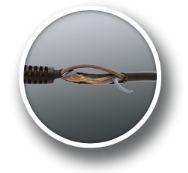
Lücke zu groß
Der Spalt zwischen dem Zahnrad und dem Sensor ist zu groß, wodurch das Signal schwächer wird.
Dieses Problem kann durch einen falsch eingebauten Sensor oder einen für den Motor ungeeigneten Sensor verursacht werden.
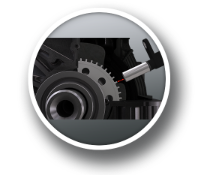
Beschädigtes Zahnrad
Das Zahnrad ist mechanisch beschädigt.
Ein mechanisch beschädigtes Zahnrad, bei dem ein oder mehrere Zähne beschädigt oder abgebrochen sind, kann eine Fehlfunktion des Signals verursachen. Daher sollte auch das Zahnrad einer Sichtprüfung unterzogen werden.
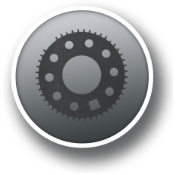
Prüfung von Nocken- und Kurbelwellensensoren
Ob der Nocken- oder Kurbelwellensensor ordnungsgemäß funktioniert, lässt sich am besten feststellen, indem man überprüft, ob das Signal korrekt ist. Ein Oszilloskop ist das richtige Werkzeug dafür.
Zunächst müssen Sie feststellen, ob Sie ein Hall- oder ein induktives Signal erwarten.
Ein guter Indikator ist, ob der Sensor 2 oder 3 Pins hat. Wenn er 2 Pins hat, handelt es sich höchstwahrscheinlich um einen induktiven Sensor, und wenn er 3 Pins hat, handelt es sich höchstwahrscheinlich um einen Hall-Effekt-Sensor. Es gibt jedoch einige Ausnahmen, manchmal kann ein induktiver Sensor einen 3. Pin als Abschirmung haben.
Eine gute Möglichkeit, NTK-Sensoren zu identifizieren, ist die Handelsnummer. Wenn diese mit "CM" beginnt, handelt es sich um einen induktiven Sensor und wenn sie mit "CH" beginnt, ist es ein Hall-Effekt-Sensor.
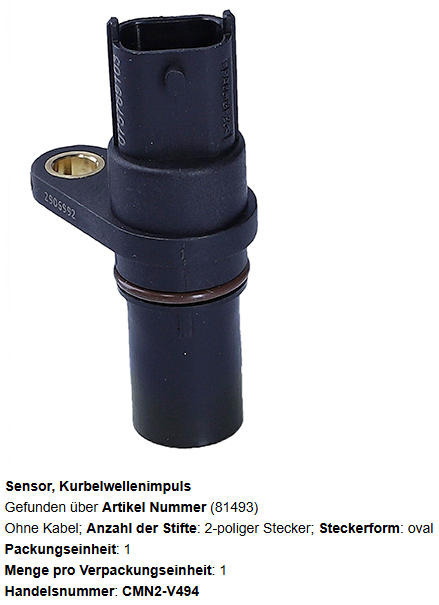

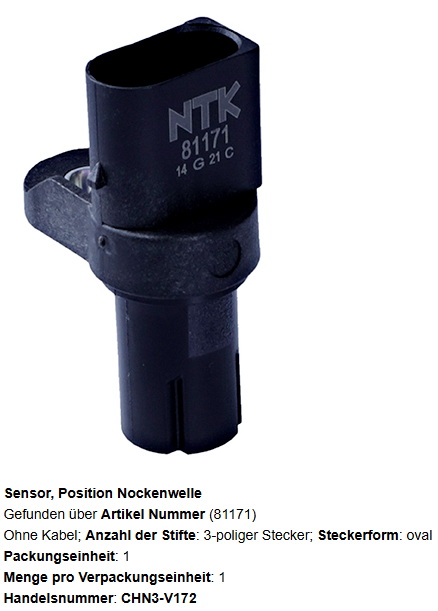
Prüfung induktiver Sensoren
- Verbinden Sie die Messausgänge des Oszilloskops mit den Pins 1 und 2 des Sensors.
- Wählen Sie die Oszilloskop-Voreinstellung so, dass Sie das Signal des Sensors deutlich sehen können. Zur Auswertung des Signals ist es am besten, zwei Kurbelwellenumdrehungen zu visualisieren. Die Einstellungen müssen mit steigender Motordrehzahl angepasst werden, damit das Signal sichtbar bleibt. Hier finden Sie einige Informationen, die bei der Einstellung der X- und Y-Achse hilfreich sein können:
Y-Achse: | X-Achse: |
---|---|
Signalspannung mindestens 0,5 V beim Start | Zwischen 100 und 200 msec, um zwei vollständige Kurbelwellenumdrehungen sichtbar zu machen |
Signalspannung mindestens 2 V bei Leerlaufdrehzahl | |
Signalspannung steigt mit der Motordrehzahl |
- Die Spannungsspitzen sollten sich bis auf die Referenzmarke nicht stark voneinander unterscheiden. Eine Abweichung von 20-30 Prozent ist für viele Fahrzeughersteller normal. Abweichungen darüber deuten auf eine Beschädigung des Impulsrades hin.
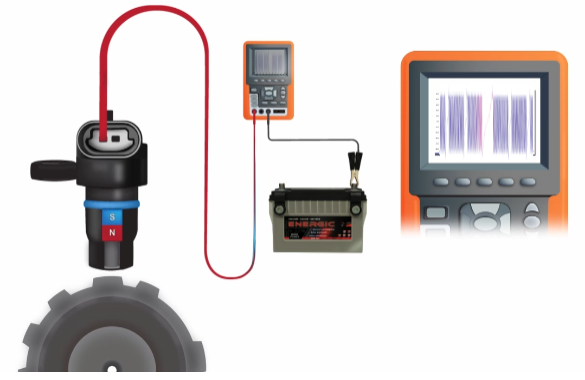
Prüfen von Hall-Effekt-Sensoren 1/2
- Verbinden Sie die Messausgänge des Oszilloskops mit dem Pin der Signalleitung des Sensors und der Batteriemasse (Klemme 31).
- Wählen Sie die Oszilloskop-Voreinstellung so, dass Sie das Signal des Sensors deutlich sehen können. Zur Auswertung des Signals ist es am besten, zwei Kurbelwellenumdrehungen zu visualisieren. Die Einstellungen müssen mit steigender Motordrehzahl angepasst werden, damit das Signal sichtbar bleibt. Hier finden Sie einige Informationen, die bei der Einstellung der X- und Y-Achse hilfreich sein können:
Y-Achse: | X-Achse: |
---|---|
Signalspannung entweder von 0-5V oder 0-12V | Zwischen 150 und 200 msec, um zwei vollständige Kurbelwellenumdrehungen sichtbar zu machen Geschwindigkeit: |
Die Zeitspanne zwischen hohem und niedrigem Pegel steigt mit der Motordrehzahl |
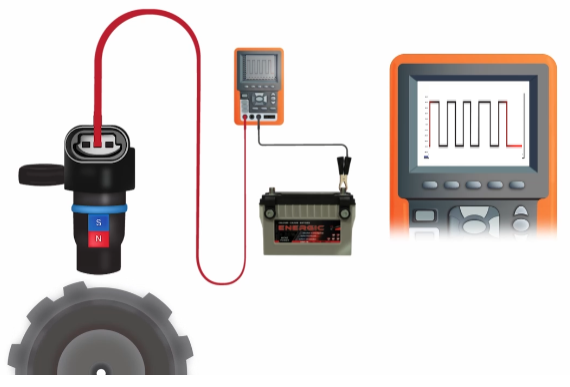
Prüfen von Hall-Effekt-Sensoren 2/2
- Wenn mit dem Oszilloskop kein Signal erkennbar ist oder die Signalspannung zu niedrig ist, liegt höchstwahrscheinlich ein Problem mit der Stromversorgung des Sensors vor. Um die Stromversorgung des Sensors zu überprüfen, können Sie die Spannung zwischen der Plus- und Minusleitung des Sensors messen. Je nachdem, ob es sich um eine 5V- oder 12V-Schaltung handelt, wird ein entsprechender Messwert erwartet.
- Wenn Sie an einem Pin der Signalleitung des Sensors kein Signal messen können und die Spannungsversorgung in Ordnung ist, ist der Sensor defekt.
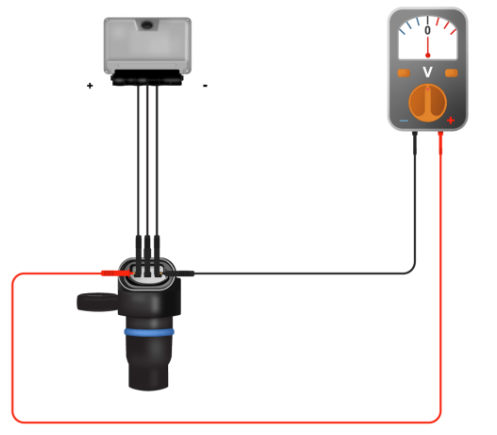
Weitere Tests der Sensorschaltung
Um dieses Ergebnis zu überprüfen, können Sie den Widerstand der Kabel zwischen dem Motorsteuergerät und dem Sensor kontrollieren. Das Kabel muss in einem stromlosen Zustand gemessen werden, um eine Beschädigung des Stromkreises zu vermeiden. Ziehen Sie dazu den Stecker am Motorsteuergerät und am Sensor ab. Der Widerstand kann je nach Kabellänge und -durchmesser variieren, aber ein Widerstandswert von ca. 1 Ohm ist ein normaler Wert für ein funktionierendes Kabel.
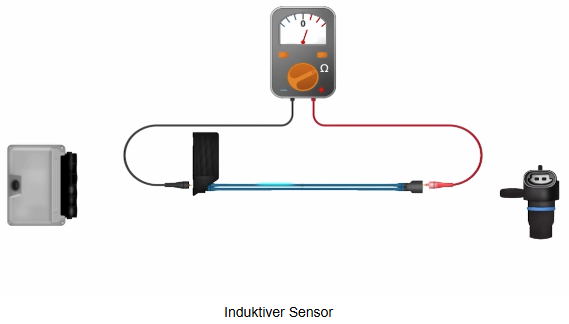

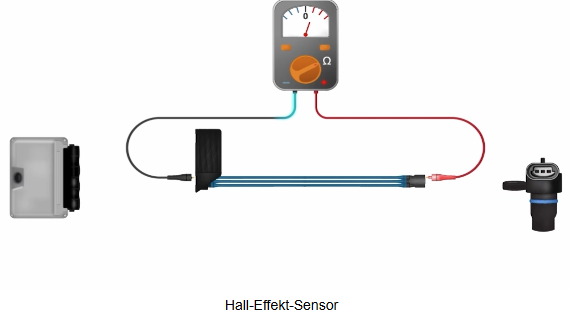